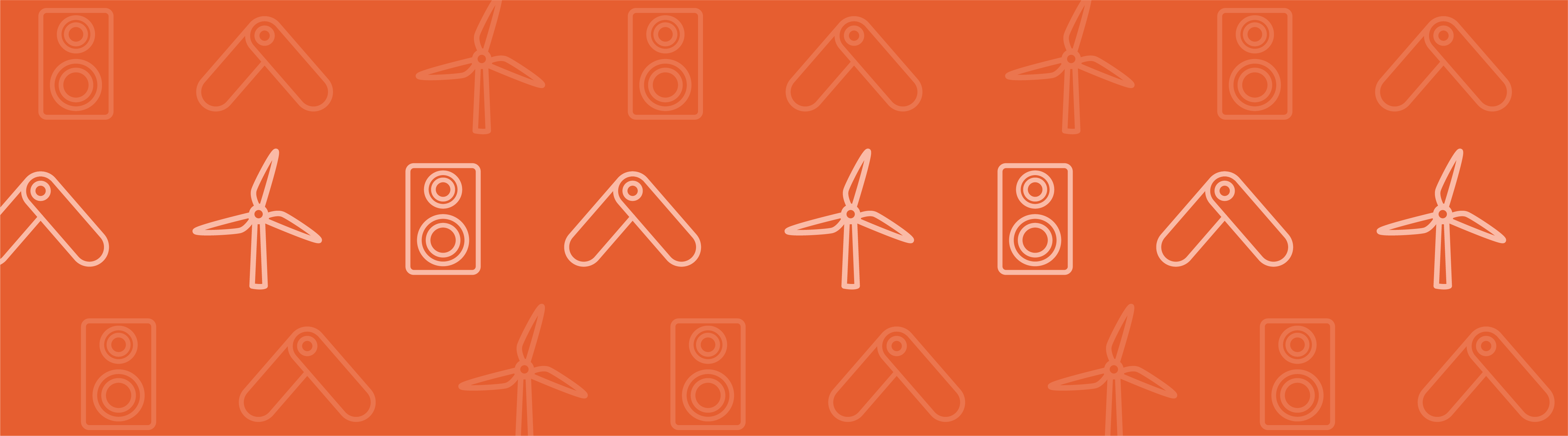
Energy and telecom cables often journey through harsh environments to reach their destinations. Some cables are responsible for carrying high currents and must navigate in conditions that include high thermal loads, mechanical loads, and limited ventilation. We recently published a story in the IEEE Spectrum Insert,Multiphysics Simulation, explaining how the Prysmian Group, a leader in developing cable systems across many industries, has begun using COMSOL Multiphysics to improve their development process, save resources, and optimize their cable designs.
A New Kind of Model
Power transmission systems need to deliver a required level of current without overheating the cables. Cable structure, internal electric losses, installation system geometry, and environmental conditions — such as the ambient temperature or the properties of the surrounding material — all contribute to system’s thermal response. Even external loads, such as those caused by solar radiation (in the case of an aboveground cable) or in proximity to other systems (e.g., other cables crossing the route), must be accounted for in the design.
While simple mathematical models and calculations suffice for many cases, cable systems are more commonly being installed in environments with many external influences that make it hard to predict performance and side effects.
That’s where multiphysics simulation enters the scene.
COMSOL Multiphysics simulation showing temperature distribution in the cross section of a double-armored umbilical cable.
Engineers atPrysmianuse the COMSOL software for optimizing the geometry and arrangements of components in their high-tech cable solutions. Such systems may require a careful combination of geometry, materials, and positioning of individual parts. For example, composite cables may contain power conductors, hoses for fluid delivery, and cables for signal transmission.
The team has carried out simulations that analyze the physical effects in individual cables and entire power transmission systems by accounting for the relevant loading and environmental conditions. This allowed them to test, in a virtual sense, their designs before building and running prototypes. In one case, they had to take mechanical loads into account and simulated impact testing in medium-voltage cables. They used their results to optimize the thickness and material choices used in the external layers.
Simulations Proved Useful
The simulations proved particularly useful for understanding the coupled structural, thermal, and electromagnetic problems that are challenging to solve. Massimo Bechis, a modeling and simulation specialist at Prysmian, comments that they’ve used COMSOL Multiphysics to “do extensive transient analyses to account for daily variations in solar irradiation and ambient temperature conditions […] multiphysics simulation really solves these kinds of problems that were very difficult or even impossible to do before.” They have simulated a range of events and phenomena, including impact testing, temperature distribution in double-armored umbilical cables, and computational fluid dynamics (CFD) analysis in high-voltage systems with limited ventilation.
Simulation results showing a thermal and fluid flow coupled analysis of a high-voltage cable system installed inside a tunnel with only natural ventilation.
Bechis explains that simulation has improved the way products are developed, and that using the COMSOL software has helped them take a big step forward in the level of services they are able to offer customers and designers. “COMSOL is able to solve these kinds of problems because we can build a parametric model to optimize the geometry, the laying of the cables, and we can include the physics needed to account for the convection in the air […] we can account for current load changes instead of considering constant operating conditions. This allows us to satisfy requests to consider transient conditions due to load changes.”
Improving the Design Process
The superb results at Prysmian show strong promise for future developments. Simulation has opened up a whole world of possibilities for design, testing, and optimization prior to prototyping. It has reduced their costs, prototyping time, the number of lab tests, and has provided a straightforward way to optimize designs ahead of time, affirming their already-spectacular product record. The team expects that these methods will eventually lead to changes not only in the design phase of development, but also in manufacturing processes.
Simulation has also given them an avenue for communicating their design choices. As Bechis concluded, “Now we are able to optimize, among other things, the structure of our cables and still meet the specifications. We can also explain why we use a certain amount of material in a certain layer and show how we came to our decisions based on the modeling […] we have improved procedures for designing our cables and power transmission systems. We have an additional and powerful way to respond to requests from clients.”
Further Reading
- Read the full story, “Simulation Software Brings Big Changes to Cable Industry” from theIEEE SpectruminsertMultiphysics Simulation.
Comments (0)