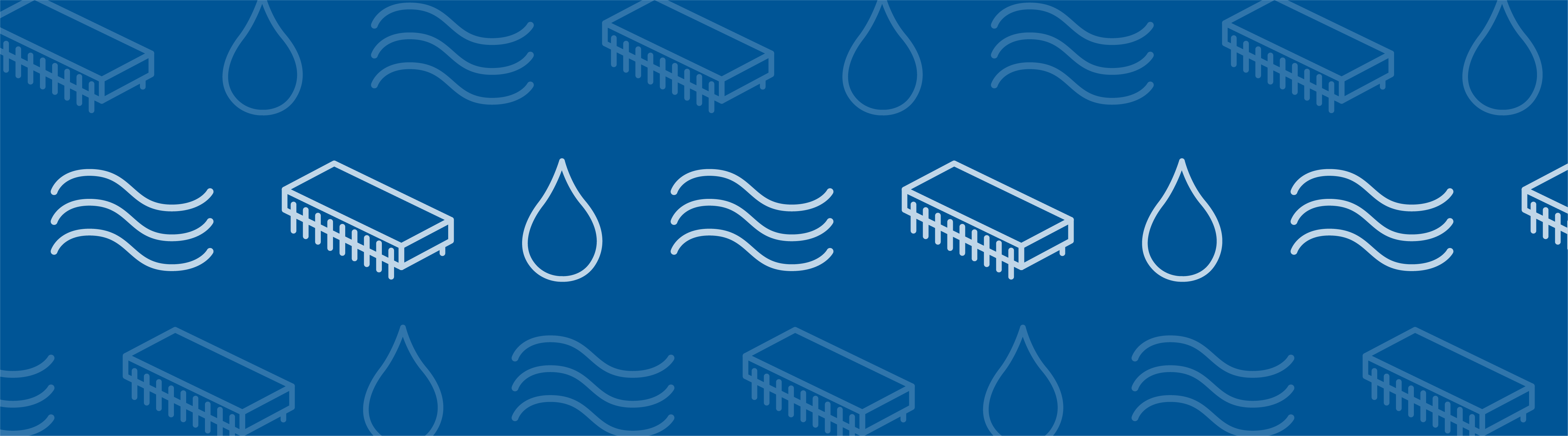
Nature is full of counter-intuitive phenomena; I’m fascinated by everyday examples like the one we talked about this summer,sinking bubbles in a pint of Guinness, but I have to say that engineering has its fair share of such examples too. The concept of heat exchange in coaxial pipes struck me as a student, as it showed me the relentless tinkering attitude typical of engineers wanting to optimize their design. In this kind of heat exchanger both streams, hot and cold, may flow in the same direction (parallel-flow) but normally engineers prefer to reverse the direction of one stream (counter-flow), as they have found it to be more efficient. The simplicity of this design idea is striking; it’s not at all intuitive for a young engineer-to-be.
Sketch of a coaxial heat exchanger.
Why Counter-flow?
Before we can answer that, we must answer another question: What is the meaning of more efficient design in this context? Well, it means that the average temperature difference along the pipes in the counter-flow case is greater than in the case of parallel-flow or, using heat transfer jargon, the logarithmic mean temperature difference (LMTD) is higher. This design enables the two streams to exchange more heat within the same pipe length (see plot below). That, of course, leads to a material-reduction and in turn lower costs.
Parallel– versus counter-flow temperature profiles.
Designing a Heat Exchanger
When designing a heat exchanger there are several parameters that need to be determined. Such as the required exchanger area, or the minimum mass flow rate that guarantees the desired temperature profile. The handling of turbulent transport properties and temperature-dependent materials should also be taken into account. Lots of handbooks, nomograms, equations, and the like are available to this aim. These tools are very helpful in the early design stage, but they lead to cumbersome, error-prone, and lengthy calculations while also relying on simplifying assumptions. In order to verify the design and optimize the proposed solution, the engineer must look to simulation.
Now let me show you how simulation can be really helpful. UsingCOMSOL Multiphysicsand thePipe Flow ModuleI solved the design problem depicted in the sketch above.
Problem Definition
Given a coaxial counter-flow heat exchanger where all its geometrical properties, fluid and solid properties, inlet temperatures, and inlet mass flow rates are fixed, which is (a) the outlet temperature of the hot stream for a length of 12, 36, 60 m, respectively; (b) the length needed for an outlet temperature stream of 73 °C? Take into account the turbulent nature of the streams, pipe’s surface roughness, and temperature-dependent material properties. Consider the fully developed streams.
After setting up the model I solved problem (a) by using a parametric sweep and problem (b) by using one of the brand newgradient-free optimization methods. The total simulation time for both problems was under 2 minutes, and you can see the results in the figures below. I’m quite happy with the results, and I didn’t have to rely on any rough simplifying assumptions. I feel confident it’s a good design.
Problem (a) solved: temperature profiles along the heat exchanger.
Problem (b) solved: the optimal length of the heat exchanger is 24.9 meters.
Comments (4)
Thomas Radtke
January 16, 2015Being still rather new to Comsol I find this blog post quite interesting. Is the model available for download? I do not fully understand how the reduced cross section of the outer pipe (i.e. the annulus) is accounted for in the pipe flow module…!? Can anyone give a hint?
Valerio Marra
January 16, 2015Dear Thomas,
I suggest to start with the models available here:
http://www.comsol.com/models/pipe-flow-module
The boundary condition realizing the multiphysics coupling you’re looking for is called Wall Heat Transfer, which is used to set up heat exchange across pipe walls. For example, you can define an external temperature and the nature of the heat transfer taking place at the wall.
Best regards,
Valerio
Thomas Radtke
January 18, 2015Valerio,
thanks for the quick reply and the pointer to the example models. I guess after a little playing I’ll figure it out. So the wall heat transfer works both ways? I was just puzzled because the natural interpretation of wall in this context is the outside wall of the pipe. That is, (ignoring heat exchange with the environment) the whole heat transfer between inner pipe and annulus is defined in the wall heat transfer if the inner pipe, right?
Thanks and best regards,
Thomas
Valerio Marra
January 21, 2015Hi Thomas,
Your intuition is correct, you’ll be able to set up a wall heat transfer that works both ways.
Valerio