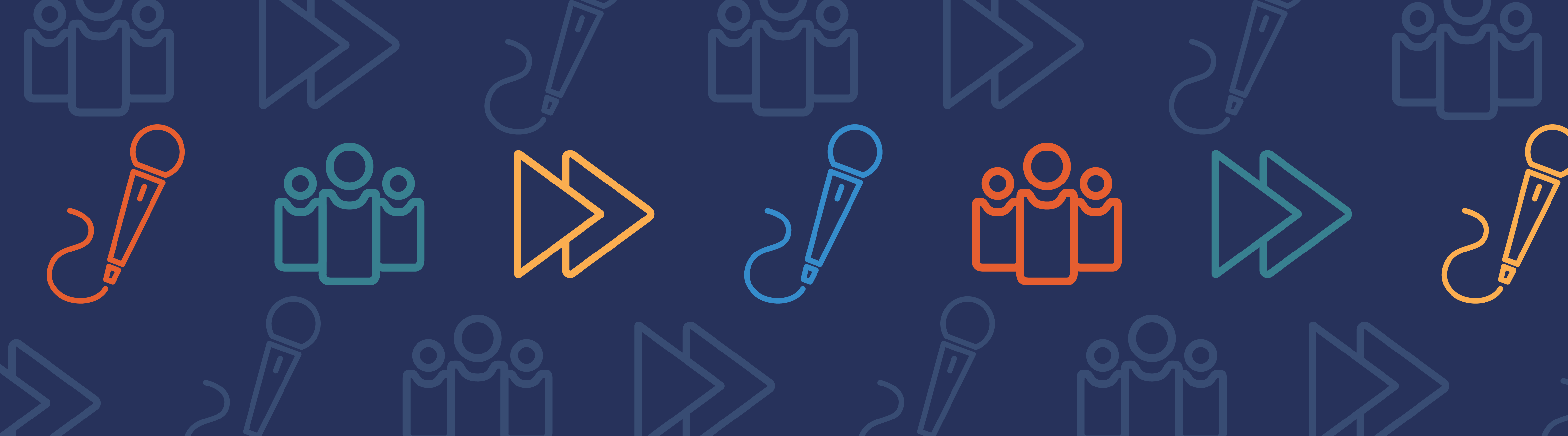
You’re listening to music when you bump into your loudspeaker, knocking it off the table. Fortunately, it still works! In his keynote presentation at the COMSOL Conference 2017 Boston, Richard Little discussed how Sonos, Inc. ensures that loudspeakers are durable enough to withstand certain stresses and how they use simulation to improve the robustness of the transducer component. If you missed his talk, you can watch the video recording below, followed by a quick summary of his presentation.
Richard Little Discusses Designing Durable Audio Transducers for Loudspeakers
Analyzing Audio Transducer Components with Acoustics Modeling
Say you just ordered a new loudspeaker. You probably have expectations about the product: It should survive the trip home; withstand falls; and, above all, it should work. As Richard Little said in his keynote talk: “Our customers expect that things just kind of work when [they come] out of the box and they don’t really have to worry about it, because that’s what consumer products are normally expected to do.”
Upholding these performance conditions is the job of Sonos engineers working to create powered wireless loudspeakers. To do so, they have to ensure the performance and durability of the many competing components in a loudspeaker. Little’s team focuses on just one of these components: audio transducers, which convert input electrical signals into sound. In his talk, Little discussed maximizing the durability of transducers via a predictive design process by accounting for:
- Fatigue
- Various environmental conditions (e.g., humidity and temperature)
- User handling (e.g., dropping)
Little and his group use simulation to effectively analyze the durability of their transducer designs. This enables them to create virtual prototypes, improve the accuracy of their physical prototypes, and reduce time to market.
Stationary Transducer Component: Basket
First, Little discussed a transducer component involving nonmoving parts that need to withstand handling-related stress: the basket. The basket of a transducer is its weakest part. As such, Little’s team works to improve transducer baskets by studying their materials and geometry. Little spoke about finding a type and grade of steel that can prevent a basket from deforming, while still minimizing material costs. This is accomplished by evaluating the basket’s structural integrity with time-dependent mechanical simulations.
From the video: Simulation results for the transducer basket with <130 MPa stress.
The results Little shared indicate that 130 MPa is the targeted yield stress. This is seen as the lowest acceptable yield strength level to use when choosing a grade of steel for a design. Of course, there are other options for improving the design’s robustness, including using thicker steel or a different plastic material for the basket. However, these design choices have implications in regards to cost, acoustic performance, and manufacturing requirements.
Moving Transducer Component: Woofer Diaphragm
Switching gears, Little discussed a moving component example involving a flat speaker that is typically placed beneath a television. Due to its design, the speaker’s woofer is shallow and the diaphragm is mostly flat. The voice coil of the woofer is subjected to a great deal of stress where it is attached to the lower diaphragm surface, because the flat diaphragm offers no geometric reinforcement.
Simulation confirms that high stresses exist in this specific location, with some areas having high enough stress to eventually fatigue and fail. The Sonos team addressed this challenge by reinforcing the area with the highest stress by gluing on a small secondary ring. This design modification removes all of the stress, while negligibly impacting cost and acoustic performance.
From the video: The woofer diaphragm design was modified by adding a second ring, reducing stress.
With simulation, Richard Little and the Sonos team managed to accurately analyze stress on audio transducers and improve their designs. “This is a great way of investigating the durability of your product, as opposed to just designing for performance,” Little said. “It’s something that has been very important for us. We want our products to last 10 years out there in the field under normal usage.”
Want to learn more about Sonos’ acoustic simulations and loudspeaker designs? Watch the video at thetop of this post.
Comments (0)