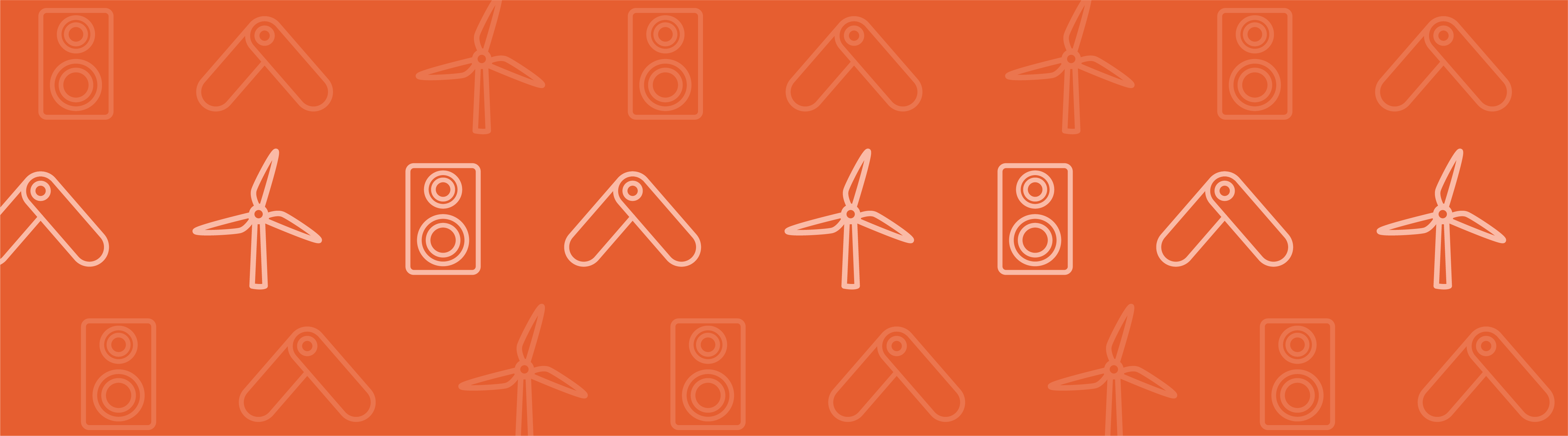
Solar energy is created by combining sunlight with a semiconducting material, often silicon. But solar, orphotovoltaic, cells require such a high-quality silicon that the manufacturing process is complicated and costly. As a photovoltaic material producer and furnace manufacturer, EMIX turned to COMSOL Multiphysics® simulation software to optimize theircold crucible continuous casting(4C) process and create the silicon needed for a more efficient solar-powered world.
Solar Energy Efficiently Powers the World
Solar energy is created whenphotovoltaic cellsmade up of a semiconducting material, such as silicon, transform sunlight (photons) into electricity (voltage). In photovoltaic cells, microthin layers of silicon make up integrated circuits that conduct electricity.
Photovoltaic cells range from a single cell to a group of cells called amodule, or a group of modules called anarray. Different amounts of solar cells can power anything from a small electronic device, such as a cellphone, to a whole building. Solar cells are used in a variety of applications, including transportation, telecommunication, space exploration, and more.
The power derived from solar cells provides a clean and sustainable source of energy; solar energy is a renewable resource. The operation of solar cells doesn’t require any moving parts or emissions, which makes them even more energy efficient.
As much as solar energy is a preferable electricity source, there are still some issues with how it is manufactured. Although the operation of solar cells is efficient, manufacturing them costs a high amount of power in itself. The silicon needed for solar cells also has to be extremely pure. The purity of silicon directly affects the amount of electricity produced from sunlight, which is an amount known as itsphotovoltaic conversion efficiency. While common metallurgical silicon is 99.9% pure, the silicon used for photovoltaic cells must be 99.9999% pure.
Multiphysics Simulation Improves Manufacturing Process for Solar Cells
To fill the need for highly pure silicon for solar cells, a research team atEMIXdeveloped the cold crucible continuous casting (4C) process, which transforms metallurgical silicon into a substance ready for solar cell use. First, silicon is fed into a water-cooled crucible and inductively heated to a melting temperature of 1414°C. Then, the silicon is electromagnetically mixed inside the crucible. Lorentz forces prevent contact between the silicon and the crucible walls.
The mixture homogenizes at the solid-liquid interface, which enhances crystallization conditions for a high purity. The melted substance is pulled through the bottom of the crucible, cooled, and solidified into a rod through an annealing process. Finally, the high-purity silicon is sawed into ingots and sold to solar cell manufacturers, where it is sliced into 200-micrometer thick wafers for use in photovoltaic cells.
The geometry of the crucible used in the 4C process. Copyright © EMIX.
EMIX has been using COMSOL Multiphysics software nearly as long as they’ve been manufacturing photovoltaic-quality silicon. Using theHeat Transfer in Fluidsinterface and theLaminar Flowinterface in the Heat Transfer Module, the research team can adjust certain variables to ensure that the 4C process optimizes production rates and is as energy efficient as the solar cells it produces.
The research team at EMIX from left to right: Julien Givernaud, Elodie Pereira, Nicolas Pourade, Florine Boulle, Alexandre Petit. Copyright © EMIX.
By simulating the 4C process, the EMIX team can test a variety of different variables, including:
- Cooling method
- Pull rate
- Crucible and coil shapes
- Characteristics of the furnace
- Effect of the electromagnetic field
- Shape of the solid-liquid interface
- Effect of elastic stresses on crystallization behavior
A simulation of the 4C process using COMSOL Multiphysics simulation software. Copyright © EMIX.
Using COMSOL Multiphysics simulation software to enhance the 4C process has proved to be extremely beneficial for EMIX. They were able to estimate both inductance and impedance in their silicon manufacturing, improve their crucible design for electrical efficiency, and test different parameters for continuous casting. This led to higher production rates, lower stresses in the silicon ingots, energy savings of 15%, and a 30% increase in pull rate.
Thanks to an innovative, optimized, and energy efficient 4C process, EMIX has been able to streamline silicon production. With simulation, they have even identified processes that they will soon test on an industrial scale. For now, we can be sure that the future of photovoltaic cells and solar energy is looking bright.
Further Reading
- Read more about how EMIX uses simulation on page 20 ofCOMSOL News2015
- Run a similar simulation: Download ourContinuous Casting tutorialto get started
Comments (0)