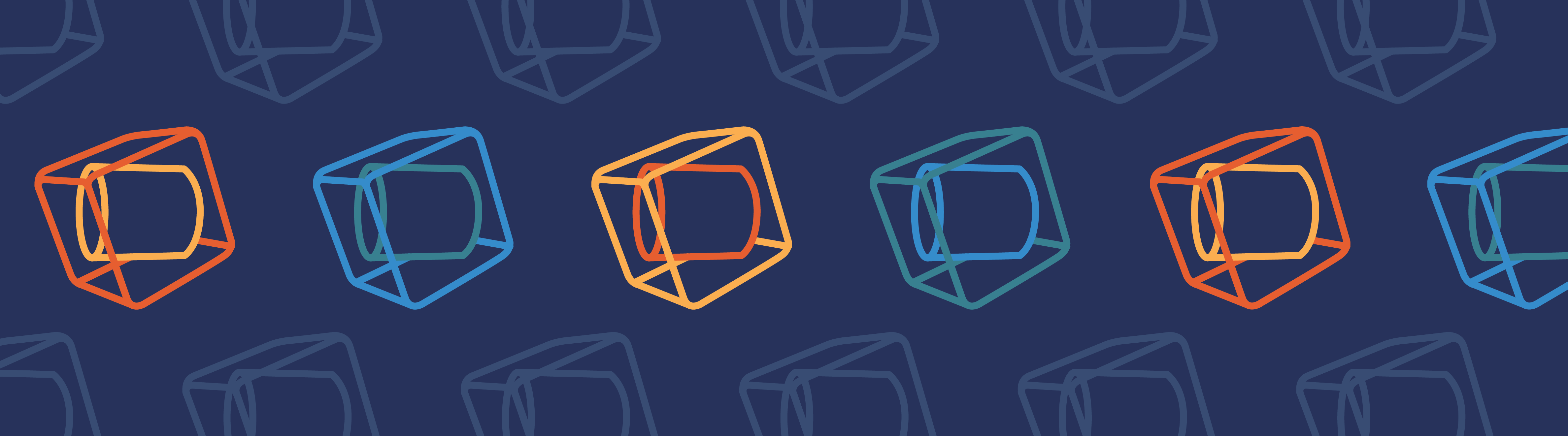
I have great news for anyone who is eager to learn the fundamentals of simulating structural mechanics in COMSOL Multiphysics. We have just published a completely revamped version of our video tutorial on the static bracket model. COMSOL Multiphysics version 4.4 and the Structural Mechanics Module are used to analyze the resultant forces, stresses, and deformations that occur on solid structures that are subjected to external loads.
Video: How to Model Structural Mechanics in COMSOL Multiphysics
Conducting the structural analysis of a model is an imperative step in the design process. The Structural Mechanics Module, an add-on to COMSOL Multiphysics, offers a virtually limitless amount of capabilities for you to do just that.
This video introduces you to the Structural Mechanics Module and walks you through the entire model-building process for setting up and solving a mechanical problem. This includes demonstrations on how to create parameters, named selections for different parts of your geometry, local variables to implement complicated expressions defined in the model, custom meshes, and tabulated results. To demonstrate the workflow for building and solving a structural mechanics problem, the COMSOL Multiphysics version 4.4 tutorial model of a static bracket assembly is used.
The smallest components, while often overlooked in design, can be the most instrumental ones. Brackets serve as a core component of support for many mechanical devices in numerous industries. In this model, a bracket assembly is fixed in place through eight mounting bolts. A load is applied on the two arms of the bracket, which is representative of a pin being placed between the holes in the bracket arms. As a result, the two bracket holes will experience a loading from this pin. After an initial analysis is complete, the direction of the pin load is varied through a parametric sweep to see the variations in force exertion, stress distribution, and deformation.
Model Download
- Shown in the video:Bracket — Static Analysis (version 4.4)
Video Transcription
Today, we will be learning how to model a structural mechanics problem, in COMSOL Multiphysics. We will conduct a static analysis of a bracket assembly, and in the end, perform a parametric sweep to analyze a bearing load at different angles. So let’s get started.
We start our modeling by opening COMSOL Multiphysics, bringing us to the New window. Here we have two options for setting up our model. Use the Model Wizard as a guide for specifying the dimension, physics, and studies you want, instead of starting with an empty model. Here we select our space dimension. When modeling in Structural Mechanics, we can work in 3D, 2D, or 2D axisymmetry, but not 1D or 0D. With our model being three-dimensional, choose 3D for the space dimension.
We are brought to the Select Physics window in the Model Wizard. Here we can add the physics that our model will exhibit. When it comes to choosing physics, this is completely dependent on the model and what meaningful information you are trying to extrapolate from the results. It is advantageous to familiarize yourself with all the physics interfaces available to you, because you may want to add more physics that are relevant to your model later on. Since we are doing a structural analysis of a 3D solid, we go under the Structural Mechanics branch, select Solid Mechanics, and add it to our model. Click Study to enter the Select Study window.
There are several different types of studies to choose from, as shown, depending on the physics interfaces used within the model. Selection of the study type is completely dependent on your analysis objectives. For example, in the case of our bracket model we want to compute deformations and stresses at static equilibrium; so the properties are time-independent. Therefore, under Preset Studies we select Stationary. After clicking Done, you are brought to the COMSOL Multiphysics desktop.
To create parameters and constants in COMSOL Multiphysics in the ribbon, add Parameters. Here we define the parameters and constants that we’ll be using later in this model, which are stored in this table.
Before we add the parameters let’s take a look at the problem we are modeling to have an understanding of where our parameters are derived from. We have a bracket, where the mounting bolts of the assembly are assumed to be fixed, and securely bonded to the bracket itself.
A pin is placed between the two holes in the bracket arms, and the inner surfaces of the two bracket holes will experience a loading from this pin. We will want to vary the direction of the pin load to see the variations in stress distribution and deformation. After an initial analysis is done with the pin load applied to the bracket holes along the negativey-axis at zero degrees, we will perform a parametric sweep of the pin load direction, starting at 0 degrees, and rotating 45 degrees, up to 180 degrees. “theta0” will be used to specify the main direction of the load, and will be the parameter used later in our parametric sweep. “P0” is the peak load intensity applied to the bracket holes. Lastly, “y0” and “z0” are the coordinates of the centers of the bracket holes. It’s good practice to use parameters instead of just the numerical values. When you change these global parameters, they will update throughout the entire model.
Creating a geometry in COMSOL Multiphysics can be done three different ways. The geometry can be manually created within COMSOL, it can be imported from a file, or you can synchronize the geometry you have open in a CAD program to COMSOL, through any of the LiveLink interfaces. In this example, the assembly of both the bracket and mounting bolts, are available to be imported. In the Geometry section of the ribbon, click Import. Change the Geometry import type to COMSOL Multiphysics file and Browse to where the “bracket.mphbin” file is stored on your computer. This should be located in your COMSOL folder under models, Structural Mechanics Module, and then Tutorial Models. Select the file, click Import, and the geometry will appear in your graphics window.
In the Model Builder Window, under the Geometry node, you can see the Form Union node which is the default setting for finalizing your geometry into COMSOL Multiphysics. Since we are dealing with a set of domains that are assumed to be perfectly bonded to each other, and will not move relative to each other, we use the default Form Union to finalize the geometry. Click Build All.
Creating definitions in COMSOL Multiphysics will help simplify your model, especially when working with large and or complicated geometries. Let’s take a look at a few of the options.
Go to the ribbon, and under the Definitions tab, in the Selections section, add a Box. Box selections allow you to create groups of geometric entities partially or completely inside the box, that would have the same features applied to them. This makes the process of changing materials, model equations, boundary conditions or constraints to different parts of your model much easier to do. In this example we want to make two box selections: the first is for the bolt domains, and the second is for the load-bearing boundaries of the bracket holes.
In the Box settings window find the Box Limits section. Here we can change the limit values which will serve as the dimensions of the box. We want to change these limit values so that the bolts are contained within the box. Under the Output Entities section, in the Include entity if list, choose Entity inside box.
Click the Wireframe Rendering button on the Graphics toolbar and we see in fact that the bolt domains are selected.
We can add a second box, or a cylinder selection to select the bracket hole boundaries, but we will instead add an explicit selection. From the level list, choose Boundary, in the graphics window, select any one of the interior boundaries of one of the bracket holes. Now we can check the box for Group by continuous tangent, and the rest of the interior boundaries will automatically be selected. In the graphics window, select any one of the boundaries of the other hole, and all four of the boundaries will be added.
Now that we’ve added selections to our model, we can define expressions for adding the boundary load. Local Variables can be used to introduce short and descriptive names for the complicated expressions defined in the model. Go to the ribbon and under the Definitions tab click Local Variables. In the table to define the load, we need an expression for the angle and load intensity, so we enter the following. The angle variable is used to help define the load intensity. This expression evaluates the radial angle, based on its position along the globalz-coordinate. Since our loading direction will change in only in theyand negativezdirections; or equivalently the 3rdand 4thCartesian quadrants, we can have COMSOL Multiphysics solve for the angle, by computing the four-quadrant inverse tangent. This enables calculating the arctangent in all four quadrants. The load that the bracket holes experience will be sinusoidal in nature, so the sine function is used. This last part of this expression is added to make sure that the load is only applied to the bottom half of each bracket hole.
COMSOL uses a global Cartesian coordinate system by default to specify material properties, loads, and constraints in all physics interfaces and on all geometric entity levels. For this model we want to define the orientation of the load applied to the bracket holes. Since the load direction will be rotating about the negativez-axis, we need to create a rotated coordinate system. In the Coordinate Systems section of the ribbon, choose Rotated System. This creates a rotated coordinate system, relative to the global system, that defines the orientation of the load applied to the bracket holes. Under the Euler angles subsection, in the beta field type “-theta0”.
COMSOL Multiphysics comes with a Material Browser, complete with built-in material properties for common materials, as well as materials for specific applications, and any materials created by you, the user. The addition of the Material Library grants users access to the entire COMSOL Multiphysics database of materials. Under the Built-In node, scroll down to select Structural Steel, click Add to Component, and we are done. The material has been automatically assigned to all domains. Here we can see the properties of the newly assigned material. You are free to create your own materials using the New Material function, and you can also use the Add Material button to stay within the main user interface.
Defining the physics and boundary conditions in COMSOL is made as easy as possible, to let you focus on what matters, the physics. To start go to the ribbon and click the Physics tab. Each selection level comes with the various physical properties that can be applied. You can learn about each physical property by adding it, and clicking the Help button in the top right corner of the window.
We first want to set the constraints acting on the structure. Since the mounting bolts are fixed in place, click on the Domains button and add a Fixed Constraint. Under the Domain Selection section from the Selection list, choose Box 1. This assumes that the bolts are rigid and the displacements are perfectly constrained. Next, we want to define the loads acting on the structure. Since the inner surfaces of the bracket holes experience the pin load, in the Physics tab, click the Boundaries button and choose Boundary Load. Choose Explicit 1 for the Selection. Under the Coordinate System Selection section, from the Coordinate System list, choose Rotated System 2, setting the load orientation with a value of “theta0”. Under the Force section, specify the Load vector with the following.
Whenever building a finite element model, we may want to customize the mesh if we anticipate that higher accuracy is needed in some parts of the model. Although we can solve this model with the default mesh, I will demonstrate how to use the mesh settings to get a finer mesh in some regions. In the ribbon, go to the Mesh tab and select Mesh 1. This shows the bracket geometry with the default Normal mesh applied. Although the elements appear as having straight sides, the default mesh used for solid mechanics problems is a second order, or quadratic, mesh. This means that the elements are conformal to the curved geometry.
We will create a second mesh and customize the mesh via the Element size parameters. Click the Add Mesh button. In the Mesh settings window, change the sequence type to User-controlled mesh. This will generate a Size sub node under our second Mesh. Click the Size node. Under the Element Size section, click on Custom. This automatically expands the Element Size Parameters window where the element parameters can be changed. Reducing the Curvature factor to “0.3″ and rebuilding the mesh, results in a finer mesh around the bracket holes. Rotating the geometry, and zooming in on a bolt, we can see the mesh is quite coarse around these small curved faces. The Minimum element size parameter is preventing the changes from the curvature factor. Reduce it to “0.005″ and rebuild the mesh. The elements around the curved edges are now smaller, but the bulk of the geometry remains relatively unchanged.
You can continue to refine the mesh manually if you want. It is also possible to use Adaptive Mesh Refinement to let the software automatically refine and coarsen the mesh, if desired. For the purposes of this example, we will continue with the default Normal mesh size setting.
We continue our simulation with creating a mesh using the default options. Go to the ribbon and in the Home tab, click Build Mesh. Then, in the Study section, click on the eye glasses icon labeled Study 1. Notice the Generate default plots check box. This will create a plot automatically, based on the structural mechanics physics, so in this case, a Stress plot will be created. To solve a stationary study in COMSOL, it is as simple as clicking Compute. COMSOL Multiphysics also defines a solver sequence for the simulation based on the physics and the stationary study type.
After a model has solved in COMSOL, it is time to postprocess the results. We will show you how to add to an existing plot, create a new plot, and extract information from the results.
Here we see the von Mises stress in the bracket and an exaggerated picture of the deformation, which is occurring mostly in the bracket arms. We also want to visualize the plot with vectors, so we can better see the pressure distribution on the inner surfaces of the bracket holes. Under the contextual Stress tab, in the Add Plot section click Arrow Surface. In the Arrow Surface settings window you’ll see an Expression section. From the menu choose Solid Mechanics, Load, and then Spatial load. In the Coloring and Style section, under Number of arrows, the default setting is 200. Increasing the number of arrows will give you a larger volume of arrows that are smaller in size, but heavier in concentration, which allows you to better visualize the load on the bracket holes. Go ahead and experiment with the number to see this yourself. Three thousand seems to give a quality visual. You can now see the load that was applied is displayed.
In this model we’ll also be interested in any displacement that occurs within the bracket geometry. To make a plot showing this, go to the ribbon and in the Results tab under Plot Group, click 3D Plot Group. This will open the newly generated 3D Plot Group 2 contextual tab in your ribbon. In the Add Plot section, click on Surface. The plot for the total displacement experienced by the bracket is automatically generated. Go to the ribbon, and under the Results tab you’ll see different dimensional types for plot groups. In this example we stick to two plot groups, but you are virtually limitless as you can make as many 3D, 2D or 1D plot groups you want for any type of visualization desired.
Because the mounting bolts are fully constrained, use a volume integration over those domains to accurately calculate the reaction forces. On the Results tab, click More Derived Values and choose Integration, Volume Integration. In the Volume Integration settings window, locate the Selection section and from the Selection list, choose Box 1 to add the bolts. Click Replace Expression here in the upper-right corner of the Expression section, and from the menu choose Solid Mechanics, Reactions, Reaction Force, and thexcomponent of the reaction force. Click the Evaluate button. Let’s do this again for theYandZcomponents as well. To save time you can edit the expression, in this case, by changing the component letter.
Click Evaluate and the results are shown in Table 1 under the Graphics window. They match what we would expect them to be; the entire load is in theydirection while negligible in thexandzdirections.
It’s often necessary to solve several iterations of a model to find the optimal properties for its design. Instead of manually changing parameter values, and resolving each time, a parametric sweep can be used. A parametric sweep allows you to change the values of a parameter by sweeping the parameter values through a range defined by the user.
Adding a parametric sweep to this model will enable us to solve for different load angles. Go to the ribbon, and in the Study tab, click Parametric Sweep. In the Parametric Sweep window, under the Study Settings section, click the plus sign button to add the load direction as a parameter. To the right of that, click the Range button to define the range for this sweep. We’ll start at zero degrees, and rotate the load forty-five degrees, up to 180 degrees. Click Add and then the Compute button to re-solve the model.
We are automatically brought back to our stress plot. In the 3D Plot Group window, under Data you’ll notice the Parameter value list. Now we have the five different solutions dependent on the angle of the load and can alternate between them by selecting the different values and then clicking Plot.
After performing a parametric sweep, you can create a table that lists the solutions for each parameter value. This way you can view the different solutions all at once. In the Volume Integration 1 node, click Evaluate and then New Table. The reaction forces at the different parameter values are computed. The reaction force in thex-direction is always zero, while theyandzdirections share the load, depending on the angle.
Comments (0)