A COMSOL Multiphysics® 3D CFD Model for Describing the Gas Exchange Through Microperforations
Modified Atmosphere Packaging (MAP) is a widely applied technology for the shelf-life extension of fresh and fresh-cut fruits and vegetables. This technique relies on modifying the gas composition inside de package by the respiratory activity of the product and the gas exchange through the package. The incorporation of microperforations (holes between 50-300 μm in diameter) in the packages may extend the potential applications of MAP systems, since it may increase the gas exchange and modulate the permselectivity through packages. In the recent years, many researchers have developed models to quantify the gas exchange through perforations and predict the evolution of the gas composition in perforated packages. As the packaging material is usually a polymeric film, the gas exchange through microperforated packages is considered the sum of two mechanisms, permeation through the continuous packaging film and diffusive flow through the perforations, with the latter contributing significantly to the overall flux. However, most of the models do not consider either the convective fluid-dynamic transfer of gas through the perforation or the spatial dependence of the gas concentration in the headspace, although it is a fact that in the surroundings of the perforation the gas concentration differs from that of the rest of the package. The objectives of this work were: i) to develop a 3D, spatial-time dependent mathematical model to simulate the gas exchange through a microperforation, considering both convective and diffusive flux, and verify the predictions of the gas evolution in an experimental system, and ii) gradually simplify the model to reduce the computation time by creating simpler geometries and equations, while maintaining the accuracy of the predictions. The developed approach is a fully coupled model combining the transport of species through the Maxwell-Stefan equations, and laminar flow by Navier-Stokes equations for compressible Newtonian flow, and considers the gas composition as a ternary mixture of CO2, N2 and O2. The model was solved using the COMSOL Multiphysics® software and the Chemical Reaction Engineering Module. The 3D physical system built was a representation of the experimental system designed to validate the model. It was composed of two cylindrical chambers, and the microperforation was located between them, allowing the gas exchange through both chambers. The upper chamber was continuously flushed with a CO2-enriched gas mixture, and in the lower chamber, that was initially filled with air was located a CO2 sensor. Atmospheric pressure values were also registered during the experiments. The initial and more complex model considers the whole system geometry, uses experimentally recorded atmospheric pressure changes as inputs, and computes the conductive and diffusive mass transport through the perforation using the Maxwell-Stefan equations. This model accurately predicts the gas exchange thought the microperforation, but, in order to reduce the computational cost, the model was gradually simplified considering that the microperforation has a circular shape maintaining the same exchange area, applying Fick’s law of diffusion for mass transfer, assuming constant atmospheric pressure, and reducing the geometry complexity by using radial symmetry. These simplifications contributed to reduce the computing time without losing model precision.
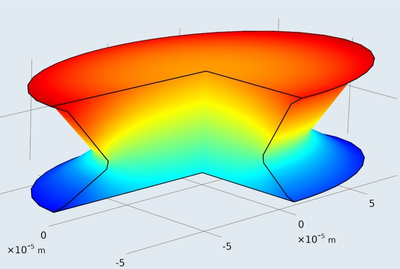
下载
- VegaDiez_5091_poster.pdf- 1.05MB