A Framework for Automated, Data-Driven Digital Twin Generation from Multiphysical Simulation Models
A digital twin is a virtual set of information replicating its physical counterpart at the utmost fidelity. Digital and physical twin benefit from bi-directional data exchange that occurs in real time and over the whole process lifecycle. Until now, experts in the design phase have predominantly used simulation and data science technologies to explore what-if scenarios. In contrast, digital twins symbolize the endeavor to make simulation insights also available to the process that is in operation, such that it might make better-informed, autonomous decisions on its own.The proposed computational framework enables the automated extraction of digital twins from existing simulation models in commercial software. Hence, it is designed to be readily applicable within the industry. Its usage is demonstrated with the derivation of digital twins that enable autonomous thermal food processing within a convection oven.
Requiring the utmost accuracy of digital twins entails setting up sophisticated simulation models to form an appropriate data foundation. To capture the product-process interrelationship better than with transfer-coefficient-based models numerously found in literature, a novel conjugate heat and mass transfer model is set up to couple porous media food processing models with the non-isothermal flow and the thermal radiation within a convection oven. Therefore, non-isothermal, turbulent fluid flow is modeled within COMSOL Multiphysics® (Non-isothermal Flow, Heat Transfer in Solids and Fluids, Turbulent Flow SST, Surface-to-Surface Radiation). Conjugate heat and mass transfer and phase change effects of the food model are implemented with several Coefficient Form PDE interfaces, the Darcy’s Law fluid flow interface and numerous variable and function definitions. Model development was performed from scratch without the usage of Application Libraries. Comparing a conjugate simulation of a food item with a constant-heat-transfer-coefficient-based simulation reveals pronounced differences: The temperature locally differs up to Emax = 48 K (30.6% relative error). The water saturations differ with Erel = 60%.
The requirement of real-time predictions reveals that digital twins must solve much faster than a simulation model. This work demonstrates how digital twins can be trained with only one-to-two training data sets extracted from multi-physical simulation models within COMSOL Multiphysics®. A proposed efficient design of experiment provides decision-support to select training data that ensure low test error of the twin on representative test data. The root-mean-square errors of the digital twin predictions are 0.30–0.83 K. This relative error of 0.18–0.49% is superior to the validation errors of the employed food processing models. Attainable speed-ups of the digital twin compared to real time are approximately Sp ≈ 3.6 × 1E4, with characteristic solution times of one-tenth of a second – without imposing a noticeable computational cost on a single-core processor. Field data with 4649 points in space and one hour of real-time processing outputs can be predicted within less than half a second.
A MATLAB® software suite called TwinLab was developed to connect simulation models, design of experiment and MPC techniques in one framework. It offers automated excitation signal generation, execution of COMSOL® models via command line mode and data extraction with method calls designed in Application Builder.
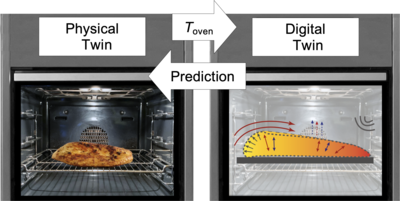
下载
- Kannapinn_6161_poster.pdf- 5.75MB