Analysis of Contact Stiffness in Hammer to Anvil Collision for Pyroshock Purposes
When dealing with space and aerospace equipment, their ability to withstand the strong excitations produced during the launch must be tested by the manufacturers according to international standards requirements. In fact, structural subsystems of the rockets are commonly released by explosive charges of pyrotechnic nature, producing strong shocks. The impulsive nature of such “pyroshocks” (as are commonly referred to) produces transient structural responses whose intensity could easily damage the carried equipment in the vicinity of the energy release zone. Hence, the mechanical resistance of these equipment must be tested experimentally as prescribed by standards such as the NASA 7003, the MIL-STD-810F, Method 517, the IEST RP Pyroshock Testing Technique and the ESA ECSS experimental standard. In these documents, many testing procedures for emulating the effect of a pyroshock in a more controlled and safer environment are described. Among the others, one of the most effective and widely used is the resonant plate pyroshock testing. The object under test is mounted on one side of a huge metal plate, which is hit by a hammer impacting on an anvil mounted on the plate, so as to provide the energy necessary to excite the item within the requirement range, commonly specified as a Shock Response Spectrum (SRS), a measure of the damage-ability of the pyroshock. In order to better understand the influence of the hammer and the anvil on the tests, simulations will be run so as to evaluate the input force (and the final SRS) as a function of the mass and speed of the hammer, as well as the contact shapes and materials.
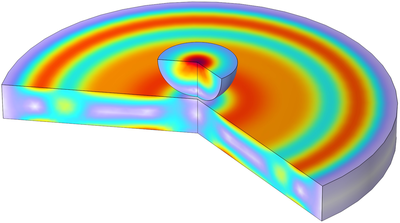
下载
- Lentini_5251_poster.pdf- 2.68MB