Approximation of the Flow Field in Electrochemical Machining Incorporating Pressure Drop Calculation
Electrochemical Machining (ECM) is a non-conventional machining technology which allows for surface structuring and shaping of metallic workpieces with high accuracy and surface quality. The machining principle of ECM is electrolysis. Hence, the mechanical properties of the workpiece material do not directly influence the machining process. Thus, even very hard materials can be machined with nearly no wear of the tool electrode. The major challenge in applying ECM is the process design. In today’s practice, this is a time-consuming and cost-intensive procedure. However, the efficiency of process design can be enhanced by applying computer simulations. This can be formulated as an optimization problem. The objective function of this optimization problem can be defined based on the workpiece shape resulting from computer simulation. Here, for each evaluation of the objective function the resulting workpiece shape needs to be simulated. It follows that there is a need for efficient ECM simulation models with low computational costs. In a previous work an ECM simulation model was developed, which encompassed the physical phenomena electrodynamics, fluid dynamics, thermodynamics, the formation and transport of hydrogen bubbles as well as geometry deformation. Fluid dynamics was regarded as a compressible two-phase potential flow. The pressure field was calculated based on Bernoulli’s equation. The total pressures at inlet and outlet were model input parameters. On that basis, the total pressure was interpolated along the streamlines in the working gap. This means, the pressure drop along the working gap was a model input parameter, which needed to be defined based on additional external information. In the present study the multiphysics model of the previous work is revisited and extended. In particular, a new submodel for approximating the pressure drop is developed for 2D ECM simulations. The submodel is built up orientated on a 1D flow model of Kozak. The total pressure is regarded as a field variable that is defined by a partial differential equation using the COMSOL Multiphysics® PDE Interface. In this equation the drop in total pressure is incorporated as a source term. The source term is defined as a function of the local Reynolds number, the local working distance between tool and workpiece and the average density and velocity in the flow cross-section. In this connection the computation of the local working distance and the averaging of local quantities across the flow cross-section is conducted by using several additional linear partial differential equations. The presented model is able to describe the influence of changes in volume flow rate and geometry on the pressure field and thus on the hydrogen volume fraction, the effective electrical conductivity, and the material removal, respectively.
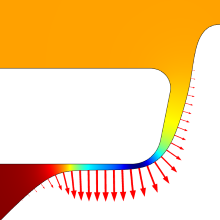
下载
- paul_poster.pdf- 0.8MB
- paul_paper.pdf- 0.85MB
- paul_abstract.pdf- 0.03MB