Assessment of the Cuttings Carrying Performance of Drilling Mud via Reelwell Drilling Method
The Reelwell Drilling Method (RDM) represents an innovative and energy-efficient approach to directional drilling (Rajabi et al. 2009; Belarde and Vestavik 2011; Breivik et al. 2020). RDM has been particularly successful in enhancing MPD and ERD. The technology enables constant well pressure profiles and reduces torque and drag, which are significant for ERD operations. RDM also facilitates underbalanced operations with heavy fluid in the well annulus, improving safety with two well barriers (Xueqin et al. 2011; Aleksandersen and Vestavik 2015). RDM's potential for deepwater drilling is notable, where traditional methods face limitations due to equipment size and weight. RDM's riserless approach allows for drilling at any water depth with smaller, less expensive rigs (JPT staff 2012; Yang et al. 2022). While RDM presents numerous benefits, it also introduces new challenges that require adaptation in well control strategies. The importance of well control during extended reach drilling has been discussed, comparing conventional methods with RDM (Veisene 2014; Li et al. 2019). Simulation studies have been performed to understand the impact of different mud densities and kick intensities on well control in RDM operations (Veisene 2014; Li et al. 2019). However, there is a notable deficiency in research regarding the impact of temperature on the cuttings carrying performance of drilling mud. Consequently, a numerical model grounded in particle flow dynamics has been developed to assess the drilling mud's capacity to transport cuttings from the bottom hole drilling areas when employing RDM. This model takes into account the effects of circulation flow rate, inclination angle, and mud temperature. The rheological characteristics of the drilling mud were derived through laboratory testing and data post processing. Two modules “Laminar Flow”and “Particle Tracing for Fluid Flow”from COMSOL Multiphysics were used for building the numerical model, where lift forces, drag forces and gravitational forces applied to particles were considered. Meanwhile, we have incorporated the temperature-dependent rheological models of drilling mud to enhance the simulation's fidelity. It is found that the three-dimensional Xiao rheological surface model, constructed from the testing data, can be integrated into the numerical model, thereby enabling the derivation of highly accurate predictions; both simulation results and laboratory findings indicate that, in directional drilling, most cuttings move and gather below the pipe's central axis; the augmentation of cuttings transport capacity due to increased circulation flow rates not only exceeds the rate of increase in flow itself but also achieves superior performance under high-temperature conditions; what’s more, the weakest cuttings transport in drilling pipes typically happens at 30° and 60° inclinations, occasionally at 90°, aligning with experimental data across temperatures and flow rates.
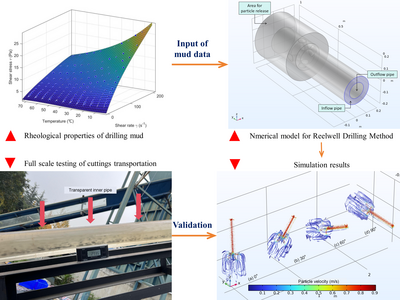
下载
- 肖飞 - Assessment of the Cuttings Carrying Performance of Drilling Mud via Reelwell Drilling Method.pptx- 3.25MB
- 地质油气 - 肖飞 - New Insights into Rheological Properties of Drilling Mud at Some Laboratory Testing Temperatures and its Cuttings Carrying Performance via Reelwell Drilling Method.pptx- 24.84MB