COMSOL Multiphysics® Model of an Industrial Top-Fired Steam Methane Reforming Reactor
Figure 1 shows a simplified scheme of a typical industrial steam methane reforming (SMR) reactor, which is a top-fired, packed-bed multi-tubular chemical reactor, consisting of a series of catalytic tubes arranged within a furnace. The tubes contain two adjacent catalytic sections filled with commercial nickel-based catalysts. The tubes are fed from above with a mixture of natural gas and steam. Thus, the direction of the process gas (syngas) is from the top down inside the catalytic tubes. The burners are located in the ceiling of the furnace and are fed with a mixture of fuel and air. Then, the combusting gas flows to the bottom, surrounding the catalytic tubes, in co-flow with the syngas. In the SMR reactor, many thermal effects take place simultaneously, mainly the endothermic SMR process inside the tubes and the exothermic combustion in the furnace. This triggers a radiative heat transfer from the furnace to the tube. The heat passes through the wall thickness of the tube by conduction and is subsequently transferred to the catalytic bed.
This work presents a model of the industrial SMR reactor. The model is implemented in the COMSOL Multiphysics® software platform, equipped with the Chemical Reaction Engineering Module. The model incorporates, at the microscopic scale, the simulation of mass transport and reaction within the catalyst particles (Reactive Pellet Bed feature). At the intermediate (mesoscopic) scale, the tube model is based on: • local mass balances (Transport of Diluted Species in Porous Media interface), • energy balances (Heat Transfer in Porous Media interface), and • momentum balances (Darcy’s Law interface). At the macroscopic level, the tube simulation is then coupled with the furnace simulation, based on local mass and energy balances, coupled with linear combustion kinetics. The furnace simulation is implemented in COMSOL Multiphysics® through a Coefficient Form Boundary PDE interface.
The model equations are integrated numerically through MUltifrontal Massively Parallel sparse direct Solver (MUMPS) of COMSOL Multiphysics®. Newton’s iterative method is adopted to solve nonlinear equations with an initial damping factor = 0.01 and minimum damping factor = 10-6. Other numerical parameters are kept by default. Tolerances of 10-3 are used as the convergence criteria of the simulation.
Figure 1 shows the simulated 3-D syngas temperature inside the catalytic bed. The syngas temperature shows an abrupt decrease at the top of the reactor, due to the endothermic effect of the fast steam reforming reactions, especially of the higher hydrocarbons contained in the natural gas. Thereafter, the higher hydrocarbons are completely consumed within a short distance, and the endothermic effects are reduced. Therefore, the heat released by the furnace combustion exceeds that required by the SMR reaction and, as a result, the furnace and process-gas temperatures increase downwards along the axial coordinate. The predictive capability of the model is assessed through validation against previous literature results and three experimental data sets obtained from a full-scale industrial SMR reactor operating from middle to high capacity.
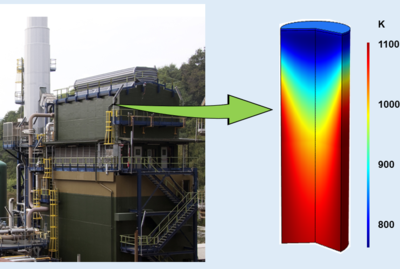
下载
- Paper_Costamagna_final.pdf- 0.49MB
- Costamagna_4341_poster.pdf- 1.66MB