Design and Simulation of Bragg Grating Based Optomechanical Sensor for Atomic Force Microscopy
Atomic force microscopy (AFM) has been widely recognized as an essential tool that enables the imaging of surface, measuring and localizing many different forces and becoming a standard technique for force spectroscopy at the nanoscale. While conventional AFM is well-developed, recent research progress in MEMS and nanophotonics give convincing performance improvements of AFM, including wide cantilever stiffness range [1], very high frequency and quality factor [2], fast and low-cost fabrications achieved in a single silicon chip [3]. Accordingly, silicon photonics has shown great potential in bringing together mechanical probes and optical cavity as compact sensors for many sensing applications. In this work, we present an optomechanical sensor based on the integration of a Bragg grating in silicon photonic waveguides with a cantilever beam on a single silicon chip for atomic force microscopy (AFM). The Si Bragg grating waveguide is designed having Si core, SiO2 substrate and air cladding. The schematic of the waveguide Bragg grating cantilever is shown in figure 1. To study the optical response of this device to a mechanical force on the cantilever tip we couple the Solid Mechanics and Electromagnetic Wave, Frequency Domain interfaces in COMSOL Multiphysics®. Briefly, first the mechanical deformation of the waveguide is determined, then 3D wave propagation is used to find the reflection of the deformed Bragg grating. The geometry was meshed with physics controlled swept mesh and element size, having the maximum element size as that of the Bragg wavelength. The solution was computed for effective mode index under boundary mode analysis, in which the numeric ports were added to the input and output of the Bragg grating. Mechanical stress of the cantilever leads to refractive index change which in turn is observed as a shift of the optical resonance in the Bragg grating reflection spectrum (see figure 2 with 1μN applied force on the tip). Our COMSOL® study shows a force sensitivity for the designed optomechanical probe of 0.03 m/N. To the best of our knowledge this is for the first time a detailed 3D, coupled finite element analysis to understand the mechanical stress induced effect on electromagnetic wave simulations. This study provides an important reference for guiding the design and experiment of the optomechanical sensors. Keywords: silicon photonics, Bragg grating, cantilever, AFM
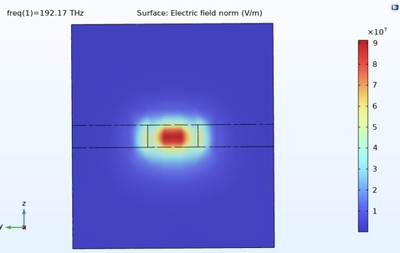
下载
- Zhang_4911_presentation.pdf- 2.01MB
- COMSOL_paper_YZ_WW_GR_17102023.pdf- 0.43MB