Designing a Structural Fastener Assembly Resistant to Vibrational Stress Using COMSOL Multiphysics®
RAKON is a worldwide expert in high performance crystal oscillator. The company decided to expand its product range to larger space equipment, the Master Reference Oscillator (MRO). This product is composed of stacked mechanical modules, joined together by structural screwed assemblies. During the launch to enter orbit, this equipment is subject to high acceleration and stress, well define by space standards and products specifications. Numerical analyses are required to ensure the design of such screwed assembly. For that, RAKON extensively assesses their devices under representative conditions. To guarantee the most realistic model possible, a precise determination of the structure’s physical parameters and an adaptation of the screwed assembly analysis methodology is required. In this paper, an experimental analysis is performed by RAKON to assess the damping behavior of the mechanical structure. The quality factors are first determined, and then numerically implemented in an acceleration spectral density (ASD) analysis model, representing the random vibrations imposed on the system. Those numerical simulations are traditionally run using legacy software, which are not always adapted for complementary analysis. The versatility of the COMSOL Multiphysics® software gives a better control of condition’s analysis. By upgrading the software’s physics readily available spring elements with rotation degrees of freedom, SIMTEC proposed a method finely adapted to RAKON’s needs. This changes in COMSOL Multiphysics® are the opportunity to validate the mechanical behavior of structural screwed assembly under vibrational stress.
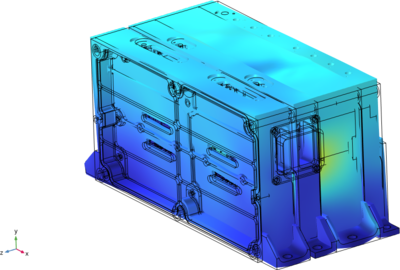