Designing and Implementation of a 4000/5A Current Transformer
This paper presents a measurement type 4000/5A current transformer which has 4 primary bars. The magnetic circuit of the prototype can be separable presenting easy installation inside the distribution panel. Time domain and frequency based simulations are obtained and the electric circuit of the primary bars is modeled separately. The finite element (FE) simulation results are then compared to real time measurements. According to real time test the modeling procedure presents an acceptable simulation environments using COMSOL Multiphysics®.
Current transformers (CTs) are vital elements in power and distributions systems and fulfill the measurement and protections tasks. Measurement and protection type CTs have basically the same structure but differ from in terms of magnetic circuit. The proposed model consists of two magnetic cores, i.e. one part is separable to maintain an easy installation without stopping the supply current. The separable part of the core is attached the other core with a spring force and the air gap during the FE simulation is assumed as 0.1 mm to see the effects of magnetic permeability, reluctance and flux linkage. The electrical circuit is seen in Figure 2. It has 4 primary bars and 2 secondary windings and external resistances are used to simulate real life environment. The proposed model is first tested electromagnetically and then coupled with Heat Transfer interface to evaluate the performance curves. Primary bars are assumed as heat source carrying 1kA each. The core material is selected as M23 type laminated sheet and related BH curve is defined in the model. Frequency response (50Hz) of current density and surface arrow lines is given in Figure 3. The model has the following simulation steps: a) It is created using COMSOL Multiphysics® and run using IBM M3 server (Intel(R) Xeon(R) CPU X5650 @ 2.67GHz, 2x12 cores). b) AC/DC Module and Heat Transfer Module are used. c) The geometry is created using AutoCAD® software. d) The core material is selected as lossy core and related BH curve is defined.
This paper presents a 4000/5A low voltage measurement type CT modeling using FE approach. Then the proposed model is compared to real time measurements. The proposed FE model is based on actual geometry and had 4 bus bars instead of using a bulk bus bar. The suggested electrical circuit is suitable for analyzing the whole model. This paper analyzes different core designs (with/without air core), primary current distribution, and electric circuitry (with different burden values), and secondary current measurement.
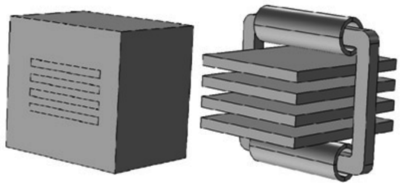
下载
- ozgonenel_poster.pdf- 0.2MB
- ozgonenel_abstract.pdf- 0.04MB