Development of Eddy Current Probe using FEM for Matte Level Detection in Pyrometallurgical Furnaces
Pyrometallurgical furnaces are used to produce metals such as copper, nickel and platinum by the smelting process. During smelting, the undesired material components are separated from the desired metal resulting in the formation of a slag and matte/metal phase. The slag phase (impurities) tends to float on top of matte/metal phase, since the density of slag is lower than the matte/metal. The molten metal/matte is then tapped out of the furnace through a tapping channel. It is desirable to monitor the level of molten metal/matte during smelting operations to optimize tapping schedules and thereby, maximize productivity. The matte/metal level is most often measured with a completely manual method, where a sounding bar is inserted into the matte/metal bath through a port in the furnace roof. This method depends on human interpretation and is thought to be inconsistent especially when different operators, on different shifts make the interpretation. In addition, the operators must have access to the furnace roof which increases safety concerns and often requires the furnace power to be switched off. This paper describes the modelling of a new eddy current sensor to be installed in the furnace sidewall for the remote detection of molten matte/metal level in the furnace using the COMSOL Multiphysics® software. The finite element method (FEM) model was designed using the AC/DC module by defining nine cylinders as numeric coils through the Magnetic Fields physics option. These coils were modelled as homogenized multi-turn conductors. A constant amplitude sinusoidal voltage (2.5 V) was applied to the drive coil. A rectangular sheet was formed at a distance of 300 mm from the coils and a partition domain was created to split the sheet into two domains. One domain was assigned as titanium metal and other as air. This was done to model the changing metal level using Parametric Sweep. Using the Frequency Domain and Parametric Sweep study options the voltage in each coil was calculated for different metal heights. The FEM model was also validated with experimental results and good agreement with experimental data was observed. The sensing system, designed with the COMSOL® software, was capable of detecting the matte/metal and slag interface at a distance of greater than 300 mm thereby, providing the potential for an automated level measurement system embedded in the furnace sidewall providing improved safety and accuracy compared with manual sounding methods.
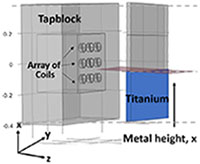
下载
- saleem_presentation.pdf- 1.59MB
- saleem_paper.pdf- 0.93MB
- saleem_abstract.pdf- 0.02MB