Elastohydrodynamics of Roll-to-Plate Nanoimprinting on Non-Flat Substrates
Roll-to-plate nanoimprinting is a manufacturing method to replicate micro- and nanotextures on large-area substrates with UV-curable resins. Figure 1 shows a schematic of the roll-to-plate imprint process, which is considered in this study [1]. It uses several rollers, for imprinting and guiding a textured, flexible stamp. The rollers are equipped with a relatively soft, elastomeric layer to ensure conformal contact with the substrate. The imprint roller (middle left) presses the flexible stamp into the UV-curable resin droplets, which have been dispensed on the substrate. The resin droplets merge and spread into a thin layer. After solidification of the resin by UV-light, the stamp is delaminated and a negative of the textured pattern is left on the substrate. The final imprint consists of the preferred texture on top of a residual layer, which should have a small and uniform thickness over the entire substrate area. The layer thickness is governed by the interaction of the hydrodynamic forces in the resin and the elastic forces of the flexible stamp and the elastomeric layer around the imprint roller. Numerical simulation of the imprint process can assist in improving the predictability and uniformity of the final layer thickness.
A schematic of the model set-up, involved physics and couplings can be seen in Figure 2. The study focuses on the flat layer thickness and the influence of textures is not taken into account. The elastic deformation of the elastomeric layer is described by linear elasticity theory. It is coupled to the pressure build-up in the liquid resin film, which is described by lubrication theory. The flexible stamp, which is treated as a tensioned web, is pre-tensioned around the roller. The elastic deformation of the tensioned web is described by the large-deflection bending of thin plates equations, considering its non-negligible bending stiffness. A Fischer-Burmeister complementarity condition captures the contact mechanics between the tensioned web and the roller. The governing equations are converted to a dimensionless format and implemented in COMSOL® via the PDE interfaces from the Mathematics Module. They combine in an elastohydrodynamic lubrication (EHL) model, which computes the pressure and layer height profiles, see Figure 3.
In previous work, the substrates were considered to be perfectly flat [2]. And there, the numerical model has been shown to be a very useful tool to assess the final layer thickness for a given set of parameters and to gain insight into their influence. But in reality, the substrates have a certain waviness. In this paper, the numerical model will be extended to capture the influence of the substrate non-flatness on the final layer height in transient and/or quasi-static simulations.
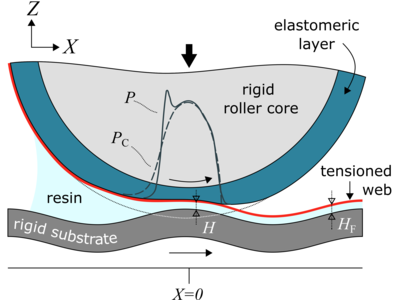
下载
- Snieder_6511_presentation.pdf- 3.08MB
- Snieder_6511_poster.pdf- 1.98MB
- Snieder_6511_paper.pdf- 1.14MB