Fully-Coupled Transient Modeling of a Highly Miniaturized Electrostatic Pull-In Driven Micropump
We present a problem-adapted finite element model, which enables the design of a novel type of a highly miniaturized, electrostatic MEMS membrane pump, as well as the investigation and the optimization of its operation. The electro-mechanical actuation scheme constitutes a strongly coupled problem with singular behavior of the electrostatic loads at small distances, and a highly non-linear mechanical contact. Additionally, fluid-structure interaction has to be included further enhancing the complexity of the model. We use COMSOL Multiphysics® as the simulation environment. In general, this software is capable to solve the above-described problem classes. The considered micropump is intended to pump air at isothermal standard conditions, and the continuous flow phenomena can be described by the incompressible and isothermal Navier-Stokes equations. COMSOL® implements these in the Laminar Flow interface. Moreover, our problem touches the so-called slip-flow regime, requiring a slip-velocity boundary condition at walls. For the structural mechanical problem, COMSOL® provides the Solid Mechanics interface, which also provides boundary conditions for mechanical contact simulations. The Electrostatics-module allows to compute the electrostatic potential as a continuous field. The Moving Mesh functionality handles the changing fluidic and electrostatic domains due to the moving structure. Finally, COMSOL® provides couplings for the different physical sub-problems. The naive combination of these different modules, however, led to unacceptable small time steps, and non-linear systems which were hard to get to converge, which is certainly also caused by the very non-beneficial aspect ratios of our device, as well as the singularity of the electrostatic interaction. Because of this, we developed a problem-adapted finite element model of the MEMS micropump, which fully couples fluid-structure-interaction with electrostatic actuation. To gain in efficiency, we reduced the 3D geometry to a 2D axisymmetric model. The key for achieving fast convergence of the transient simulations, however, is the electro-mechanical pull-in simulation, which comprises a complex and highly nonlinear contact problem. In order to tackle the convergence problems arising from that, we implemented a semi-analytical compact, but still locally distributed modeling approach for the electro-mechanical coupling and the mechanical contact model. This reduces the number of degrees of freedom drastically, and allows for larger time step sizes in the transient analysis as well. This way, we achieved stable convergence behavior and higher computational efficiency, while at the same time causing only very small approximation errors. Hence, the derived model allows to carry out parameter studies with a view to trade-off considerations between different key parameters and to identify sweet spots of the pump chamber’s performance, with a view to specific applications and specifications. For the specific pump chamber investigated in this work, we were able to identify weaknesses of the first manufactured variants, which showed a limited pump rate and error conditions in experiments that have not been fully understood, yet. It revealed, that these are caused by trapping of fluid within the pump chamber caused by geometrical deficiencies of the first design. With the help of the new and computationally efficient model, we were able to optimize the design by introducing a novel electrode shape, which prevents the effect of fluid trapping, while still maintaining a sufficiently high flowrate.
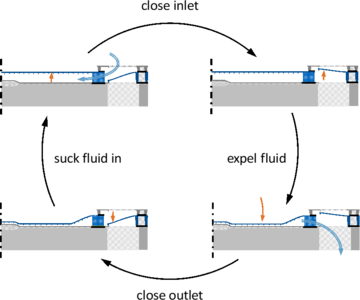