High Speed Inductive eRPS Sensor Error Reduction Using COMSOL Multiphysics®
Modern electrical vehicle motors require a precise current control over the rotation of the rotor. These motors have high performance, but their control requirement impose a precise knowledge of the rotor angular position. Rotor position sensor (RPS) are traditionally designed using magnets which are dependent of complex supply chains. The present study is dedicated to a magnet-less inductive RPS dedicated to electrical motors (Inductive eRPS), and thus able to provide rotor position at high speed. The present analysis showcases the design process of a new Inductive eRPS. The design process uses numerical simulation to optimize the sensor accuracy under realistic component assembly conditions. A numerical model is proposed by SIMTEC to investigate different realistic assembly imprecisions. It solves the Maxwell-Ampère equation in the air, the target, and the coils. The magnetic vector potential is used together with the magnetic scalar potential for the sake of efficiency. Thanks to experiments run at CONTINENTAL Automotive, the angular error prediction precision is assessed thoroughly, and the numerical model is validated for industrial use.
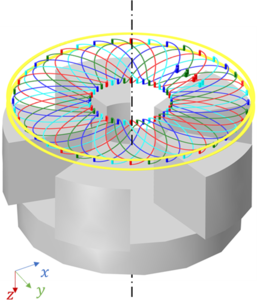