Modeling of the Reduction Stage during the Continuous Refining of Copper in a Packed Bed Reactor
Throughout history, the copper pyrometallurgical processes have been carried out mostly in discontinuous or batch systems. In recent decades new continuous technologies have been developed but focused only on Smelting and Converting stages leaving aside the Refining one. In 2002 a novel technology was proposed by the Department of Mining Engineering of Chile University which consists in two cylindrical packed bed furnaces in cascade for treating molten blister copper from converting contains around 0.01 and 0.5 mass % of dissolved sulfur and oxygen, respectively. The first furnace, containing a refractory packed bed has the function of removing the sulfur until about 0.0025 mass % as SO2 using a countercurrent airflow, while the second furnace, containing a coal or coke packed bed that of reducing the oxygen to around 0.15 mass % as CO, CO2 and H2O(g). The proposed technology has both investment and operating costs lower than those of the traditional rotatory refining furnace one. Besides it is characterized by increasing the kinetics of refining and decreasing the amount of fugitive combustion gas emissions. Figure 1 represents a schematic drawing of the reduction stage for the new technology. The purpose of the present work was to model this technology at a laboratory scale during the reduction stage in order to obtain both design and operational optimum scaled parameters for the actual pilot-industrial plant. The modeling allowed investigating the profiles of oxygen concentration and copper flow during the reduction stage inside the reactor, which represents essential information for an optimal packed bed condition of the actual pilot-industrial furnace and for the future industrial furnace design. Figure 2 shows the experimental array at laboratory scale. The modeling considers a random mono-sized spherical graphite packed bed in a cylindrical container with a stationary gravitational flow of oxidized copper. The system considers a first order kinetic law regarding to oxygen concentration. Figure 3 shows the 3D packed bed geometry, it was created by using a soft spherical algorithm in MATLAB® and then exported to COMSOL Multiphysics for its simulation. Four experimental parameters were investigated; the initial oxygen concentration in copper, the packed bed height, the furnace outlet diameter and, the diameter of spheres. Figure 4 shows some results of the CFD simulation, they correspond to the copper flow lines (left) and the profile of oxygen concentration (right). The modeling results were corroborated through experimental tests at 1473 K in a laboratory scale electric furnace, feeding it with industrial molten oxidized copper. The obtained refined copper from each experiment was analyzed by Inductively Couple Plasma, ICP, and the information was fed back to the CFD model for its optimization. The model will be scaled and used to run new computer simulations in order to predict optimum design and operational parameters for the actual pilot-industrial plant.
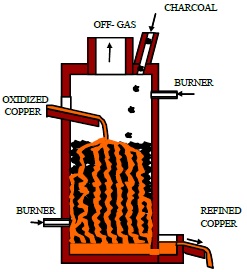
下载
- mansilla_paper.pdf- 0.59MB
- mansilla_abstract.pdf- 0.46MB