Modeling of Thermal Expansion of a Material During its Cooling Using COMSOL Multiphysics®
In metallurgy, the use of numerical models is popular because of the many coupled physical phenomena that occur during the various processes. For instance, the resulting shape and metallurgical state of a material are very sensitive to changes in temperature. The drop in temperature of the ingot during cooling leads to thermal contraction and loss of contact between the ingot from the crucible wall leads to poorer cooling. To better understand these issues, a 2D axisymmetric model is developed using the COMSOL Multiphysics® software to simulate the casting and cooling of an ingot in a crucible. The casting process is carried out until the ingot has reached its final height, and then the ingot is cooled for several hours by water flowing over the crucible walls. By using a deformed geometry to describe the growth of the ingot, a thermo-mechanical model is built. After numerical validation, this model can be used to predict the influence of thermal contact resistances at the external walls of the ingot on the temperature and shape evolution of a material during casting.
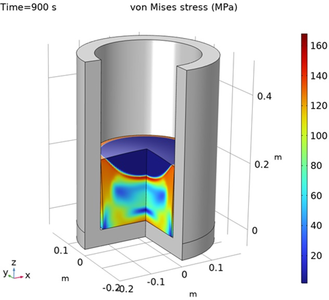