Optimal Design of Baking Plates for an Inductive Wafer Baking Oven
Baking is a central production step in the industrial production of edible wafers and waffles. The initially liquid batter is heated with a pair of metallic baking plates. Establishing a uniform and accurate temperature at the baking face (inner baking plate surface) is crucial for product quality. Traditionally, the baking plates are heated by an array of gas burners. Recent developments are aiming at a technology transition to induction heating. Its main advantages are the absence of contact between the product and the flue gas and increased efficiency. However, the highly localized heat input into the baking plates and restrictions concerning the positioning of inductors can lead to non-uniform heat profiles within the baking plates and inhomogeneous products.
A COMSOL Multiphysics® finite-element model serves to identify crucial design parameters and develop strategies that ensure the desired product quality. The analyzed problem involves induction heating, phase change, conductive, convective, and radiative heat transfer. To reduce the computational effort, a computationally less expensive model is derived and expressed via the Heat Transfer in Solids module. The 2D simulation domain represents a cross-section of the baking plate. Along the direction normal to this cross-section, which is the motion direction, uniformity of the temperature is assumed.
The reduced model is used to optimize the thickness of the baking plates for an inductive rolled wafer cone oven. The objective function depends on the oven's start-up time and the baking face's temperature inhomogeneity. Increasing the thickness of the baking plate improves the uniformity of the temperature but, at the same time, increases the time it takes the oven to reach its operational temperature. The start-up time is proportional to the enthalpy change from ambient to operating temperature. This enthalpy change grows linearly with the thickness of the baking plates. The temperature homogeneity on the baking face is evaluated in terms of temporal and spatial variations, which are shown to be both inversely related to the thickness of the baking plates. Finally, approximating the objective function (surrogate optimization) is used to find a parametric expression for the optimum based on the trade-off between start-up time and temperature homogeneity.
In earlier work, the heat transfer coefficients for the convective boundary conditions were identified from measurements on the industrial plant. At the baking face, constant thermal conductance is assumed. The finite-element model was used to study steady-state operation, start-up from ambient temperature, and transient baking cycles. Moreover, the effect of considering a nonlinear specific heat capacity for the batter phase transition was explored compared to a linear heat capacity with a heat sink.
To summarize, this contribution shows how to reduce the computational complexity of a multiphysics problem by a divide-and-conquer approach. The design optimization methods presented in this contribution are transferable to other multiphysics problems where the different phenomena occur sequentially, i.e. can be decoupled.
Keywords: Process control, Induction heating, Optimal design, Parametric optimization.
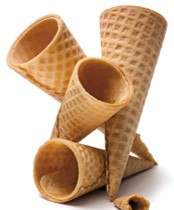
下载
- Steinbach_5431_presentation.pdf- 1.13MB
- COMSOL_Paper.pdf- 0.73MB