Optimization of the shape of material for improving the power output of thermomagnetic oscillator
Optimization of the shape of material for improving the power output of thermomagnetic oscillator Shivam Shukla a and Deepak K a,* a Department of Metallurgical Engineering, Indian Institute of Technology (BHU), Varanasi – 221005 *Corresponding author : deepak.met@iitbhu.ac.in
Abstract The world's energy needs are substantially increasing day by day and shifting towards renewable resources for energy production. Waste heat is an inevitable and infelicitous product of a large number of industrial processes. The technologies that can convert waste heat into useful energy output are being explored in recent times. They are based on the functional response of materials such as, piezoelectric, thermoelectric, thermomagnetic, etc. A Thermomagnetic Oscillator was developed recently [1] to extract electricity from waste heat. The schematic and the experimental setup of Thermomagnetic Oscillator (TMO) is shown in Fig. 1, which comprises of a cylindrical thermomagnetic alloy that oscillates between the heat source and heat sink due to the temperature gradient and the magnetic force from a permanent magnet. The electricity is generated due to the oscillation of the thermomagnetic alloy. The most important step that controls the frequency of this oscillator and power generation is the heat transfer between the heat load/sink and the thermomagnetic alloy [2]. To achieve better power output and frequency of oscillation, we have modified the shape of the thermomagnetic alloy inside the oscillator. We have designed the thermomagnetic alloy in the shape of a cylinder with fins and a spirally rolled cylinder. These shapes (Fig. 1-2) provided us better results compared to the bulk alloy cylinder and our output power has increased significantly. We have performed simulations for the described experiments in COMSOL Multiphysics software in version 6.1 using AC/DC Module, Structural Mechanics Module, Heat transfer Module and CAD Import Module Using the above mentioned modules, following physics interfaces in COMSOL software that have been utilized for time dependent study were Magnetic Fields (mf), Solid Mechanics (solid) and Heat transfer in solids and fluids (ht) For achieving desired results, moving mesh feature was used for thermomagnetic alloy. For combining the simultaneous effect of gravitational force and magnetic force, both physics i.e. solid mechanics (solid) and magnetic fields (mf) were coupled together. Hence, in multiphysics interface, magnetomechanical forces (mmf) were integrated into simulation model. The following model (Fig.3) was set up and suitable boundary conditions were applied to attain optimum coil voltage (mf.VCoil1). Here, mf.VCoil1 is a performance parameter of this model which stands for the induced voltage inside the coil during the oscillation of thermomagnetic alloy. We have optimized the performance of thermomagnetic oscillator with these simulations and that correspond to our experimental results. This device has potential applications in various industries for the harvesting electricity from waste heat.
References [1] K. Deepak, V. B. Varma, G. Prasanna, and R. V. Ramanujan, “Hybrid thermomagnetic oscillator for cooling and direct waste heat conversion to electricity,” Appl. Energy, vol. 233–234, 2019 [2] K. Deepak, M. S. Pattanaik, and R. V. Ramanujan, “Figure of merit and improved performance of a hybrid thermomagnetic oscillator,” Appl. Energy, vol. 256, 2019
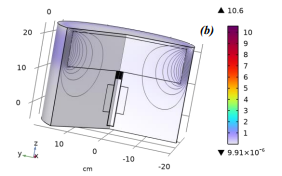