Radiation Damage in a Power Dump
In applications like nuclear reactors or particle accelerators, mechanical components near a source of radiation develop radiation damage. This typically means a change in tensile properties and fracture toughness, which depends on the radiation dose (commonly measured in ‘displacements per atom’, or DPA). In addition to such radiation hardening, radiation damage can also cause swelling, which in turn can lead to additional stresses. These effects need to be taken into account in the design of components, to make sure they do not fail.
Here, we needed to assess the risk of failure for a power dump. The purpose of this power dump is to absorb gamma radiation emitted from a target that is irradiated by an electron beam, but it also stops many other types of radiation (neutrons, electrons, positrons). The material of which this component is made can become very brittle after irradiation, so fast fracture is the most likely failure mechanism we need to assess here.
To ensure the structural integrity of this component in this environment, we used the COMSOL Multiphysics® software in combination with Monte Carlo radiation transport codes. Our approach consisted of first modeling the irradiation parameters of the system using a radiation transport code (FLUKA). From this we obtained the heat load and radiation damage production (DPA/s). We then mapped these spatially dependent results to a 3D COMSOL® model. The Solid Mechanics interface allowed us to easily implement a model for the swelling strain in addition to the thermal strain. Using this model we assessed stress-distributions over time. Some changes were made in the design in order to minimize stresses. We then assessed and evaluated conservative fast-fracture criteria, allowing us to conclude that the component is not likely to fail.
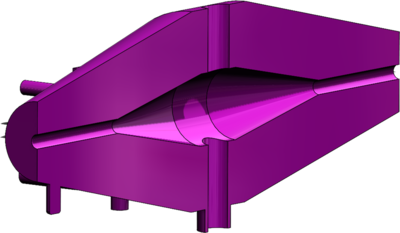
下载
- Sruijtenburg_6401_presentation.pdf- 4.41MB
- Spruijtenburg_6401_poster.pdf- 2.64MB