Study of the Process, Design, and Operating Parameters Effect on the Efficiency of the Process Mill
This study is to investigate the velocity pattern and the velocity magnitude of the cuttings that is being processed in the process mill as a result of the rotating hammers. The process mill consists of a horizontal cylindrical shell equipped with renewable liners and rotating hammers for milling of drill cuttings.
An F.E model of the process mill was constructed using dimensions similar to the actual process mill. COMSOL CFD module was used and the physics interface used is Rotating Machinery Laminar flow (rmpf). The Frozen Rotor study was employed in simulation. The model was simulated under the current operating conditions of the process mill and was referred to as the reference simulation. This gave us the basis for comparing the various effects on the relevant parameters on the process mill. The study revealed that, the hammer design (number of hammers, hammer thickness, distance and angle between adjacent hammers) is a critical parameter that affects the velocity distribution of the cuttings inside of the process mill. Thus as the number of hammers increases, the velocity magnitude increase which in effect increase the uniformity of the velocity distribution and the efficiency of the process mill.
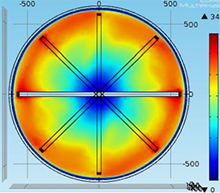
下载
- farouk_poster.pdf- 0.41MB
- farouk_abstract.pdf- 0.5MB