Thermo-Hydrodynamic Simulation of Laser Welding in Lap Joint Configuration for Dissimilar Metals
Autoliv Livbag is a company specialized in the development and manufacturing of gas generator for airbags based on pyrotechnic and compressed gas technologies. In this context, specifications of the product are very particular. Indeed, the gas generator needs to be airtight for several years despite the high pressure stored gas inside, and it must quickly open when the airbag is needed. To fulfil these requirements, a very thin disk of metal is welded on the nozzle of the inflator by keyhole laser welding. In laser welding, the final shape of the weld bead is the result of the dynamic behaviour of the keyhole and the flow of the liquid metal. This process involves multiphysics phenomena that we model to understand and improve the operational parameters of this welding process. The lap joint configuration in laser welding of dissimilar metals is modelled to study the dynamic behaviour of the keyhole and the shape of the melted area. The two metals involved in this welding are Inconel 600 and DC04 steel. A three-dimensional model is built with different meshes for different physics to reduce the computational cost. The CFD and heat transfer equations are used to compute the momentum and the energy evolution. As the model should contain two metals, both in solid, liquid, and gaseous state, the Level-Set method is used to track the interface between metals and gas, and a dilute species transport equation is used to track the two metals in liquid and solid states. Metals are considered as fluid all over the computational domain and the solid phase is modelled with a Darcy’s law, derived from porous medium. Laser is modelled thanks to a source term in the energy equation and the generation of vapour is modelled by an equivalent recoil pressure applied in the momentum equation. To validate the simulation, cross-section micrography of weld bead and Energy Dispersive Spectrometry (EDS) mapping are realized. Dimensions and behaviour of the melt pool are validated by a high-speed camera visualization of the process. All experimental data are compared to the results of the simulation and show good accordance with the shape of the melted zone and the mixing of the two metals.
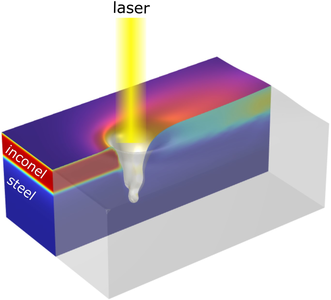
下载
- LeMener_5241_poster.pdf- 0.57MB