Using of General Extrusion Operator in Heat Transfer Applications
In this paper, the COMSOL Certified Consultant BE CAE & Test shows as the general extrusion operators can be successfully used to simulate thermal transfers in an industrial rotating furnace. Heat transfer in translating and rotating furnaces is a topic of high interest in several industrial fields, such as glass production, food industry and treatment of metals. Movement of the pieces is often needed in continuous production lines. At a chosen instant, the product thermal level depends by the residence time already spent inside the furnace as well as by the heating conditions encountered by the object along its path.
Numerical models based on a moving mesh approach can be applied to simulate thermal transient in such applications. However, this method involves in very heavy models to manage it is not always achievable in complex industrial applications. Since a few years, an innovative feature available in COMSOL Multiphysics® can be applied to solve transient thermal analysis of translating or rotating object inside a furnace. It is labelled as General Extrusion Operator (geneext). The genext can be defined as a mathematical operator allowing to map variables from a source geometry element to a destination one. This flexible feature can be exploited for a large variety of applications, being the genext suitable to map and project any variable, including the dependent variables of several physic interfaces in COMSOL®, such as the temperature in the Heat Transfer Module. Our study is devoted to present how manage this feature in a COMSOL® model built to reach this goal. A radial series of identical geometrical entities (pulleys), arranged inside a circular-shaped control volume (furnace), is considered as domain in the physical interface node when running a sequence of transient solution studies. Being the piece velocity lower and lower with respect to the forced ventilation magnitude inside the heating furnace, permanent convective fluid flow conditions are considered to provide heat transfer to the “advancing” pieces, together with radiative heat supplied by radiating tube arranged close to the roof of the chamber. At the end of each study, the temperature field solved on a specific domain (one of the pulleys) is used as initial condition in the forward active domain (next pulley, relating to the rotational direction) exploiting the genext operator functionality. This procedure leads to simulate the incremental heat exchange between each piece and the furnace, depending on the progressive time spent / location occupied by the pieces inside the furnace in working conditions.
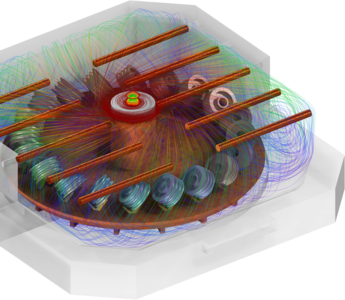
下载
- Petrone_6091_poster.pdf- 5.76MB