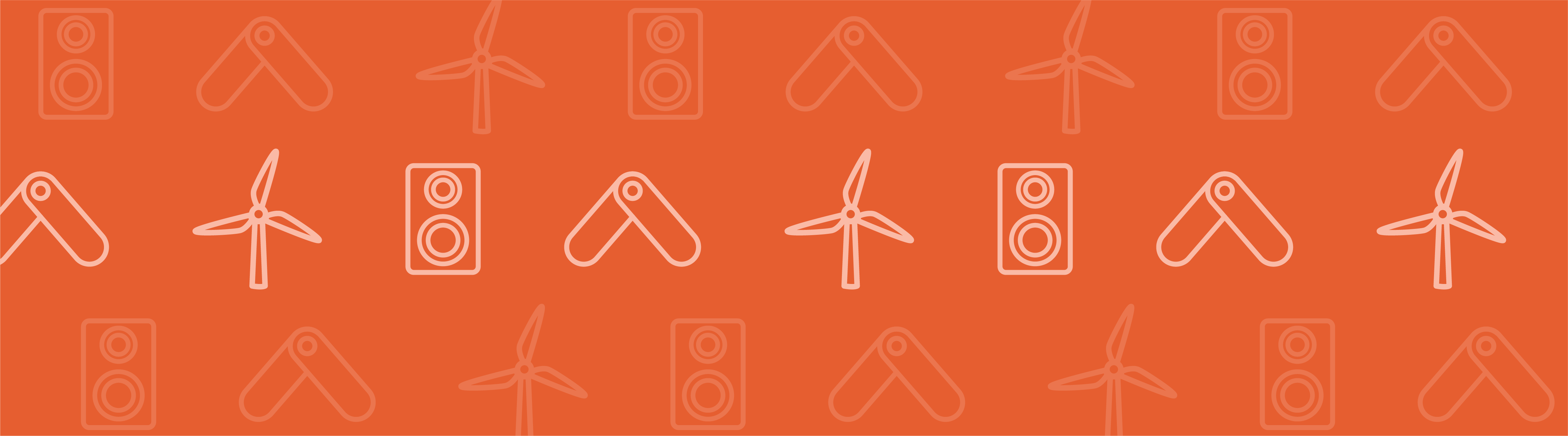
今天,我们将介绍结构力学中残余应力的概念,并以金属拉深工艺为例,了解如何计算残余应力。我们以一个经过或未经过加工硬化的弯曲梁为例,先解释如何计算和分析残余应力,然后介绍一个钣金成形模型。
什么是残余应力?
残余应力是指塑性结构卸载后仍然存在的自平衡应力。在机械零件的制造过程中,会引入残余应力,并将影响零件的疲劳、失效甚至腐蚀行为。
实际上,不受控制的残余应力可能会导致结构过早失效。尽管残余应力可能会改变性能,甚至会导致制造的产品故障,但是一些应用实际上是需要它们的。例如,像智能手机屏幕的玻璃这样的脆性材料,在制造过程中通常会在表面诱发压缩残余应力,以避免裂缝尖端的扩散。
因此,残余应力在整个力学应用中发挥着重要作用。只有通过对这些应力进行定性和定量分析,才有可能确定最适合特定应用的加工工艺。这些分析还可以帮助探索用于产品可靠性的最佳材料用量或最合适形状设计,以避免故障和失效。
纯弯曲下的梁
以下图中的细长梁为例来说明。这个梁的截面为矩形,深度为a,宽度为b。梁的左侧被固定,并在自由端上施加一个弯矩。
计算残余应力
根据梁理论,在这个示例中,弯矩是恒定的,应力可以写为:
(1)
{I_z}y
其中,I_z是关于z轴的惯性矩。
随着M_\mathrm{b}的增加,梁首先表现为弹性行为,但在达到它的屈服弯矩M_y后, 开始表现为塑性行为。由此产生了弹塑性截面。当塑性区扩展到整个横截面时,就可以确定梁所能承受的极限弯矩M_\mathrm{ult}。本文,我们假设梁在这样的时刻会坍塌,并具有完美的塑性行为。
梁的外层纤维将首先达到屈服点,而核心纤维则保持弹性。因此,由上述应用于梁外层纤维的方程推导出第一个屈服弯矩:
(2)
其中,\sigma_\mathrm{yield}是屈服应力。
在一个弹塑性弯矩下,M_\mathrm{ep} < M_\mathrm{ult},在梁的每一侧,塑性区沿厚度传播的距离为h_\mathrm{p},如下图所示。
矩形截面梁的塑性区穿透。
总弯矩可分为弹性部分M_e,和塑性部分M_p,这样:
(3)
其中,I_\mathrm{e}=\frac{a(b-2h_\mathrm{p})^3}{12}是核心的弹性区域沿z轴方向的惯性矩。
结合最后两个表达式,得到以下等式:
(4)
当来自M_\mathrm{ep}的完全弹塑性梁卸载时,梁的横截面上存在残余应力状态\sigma_r。在弹性弯曲应力\sigma_\mathrm{e}恢复后,梁试图恢复其初始形状M_\mathrm{ep}。这里,我们假设在\sigma加载后,发生的纯弹性卸载对应于弹塑性应力状态 。残余应力可以由弹塑性应力和纯弹性应力之差计算,这里的纯弹性应力指如果没有塑性行为将会产生的应力。
(5)
由弹性弯曲理论,可得到恢复的弹性应力:
(6)
=\frac{2\sigma_\mathrm{yield}}
{b}\left[1+\frac{2h_\mathrm{p}}{b}
\left(1-\frac{h_\mathrm{p}}
{b}\right)\right]y
假设出现完美的塑性行为,塑性区的应力\sigma(换句话说,\frac{b} {2}-h_\mathrm{p} \le |y| \le \frac{b}{2})保持不变,等于\sigma_\mathrm{yield}。因此,根据方程(5),残余应力可以写成:
(7)
-\frac{2\sigma_\mathrm{yield}}{b}\left[1+\frac{2h_\mathrm{p}}{b}
\left(1-\frac{h_\mathrm{p}}{b}\right)\right]y
在弹性区(换句话说,0 \le |y| \le \frac{b} {2}-h_\mathrm{p}),根据梁理论推导出的施加应力为:
(8)
因此,可以推导出残余应力为:
(9)
{b-2h_\mathrm{p}}-\frac
{2} {b}\left[1+\frac{2h_\mathrm{p}}{b}
\left(1-\frac{h_\mathrm{p}}
{b}\right)\right]\right]y
请注意,在移除外部力矩后,由于塑性变形,梁仍将具有一些永久位移,但也将恢复一些峰值载荷下的位移。如果你想要实现可控的塑性变形,这种回弹效应很重要。
在对梁进行二维建模时,我们可以选择一个采取泊松比 的平面应力假设 ,与一维梁理论相匹配,因为一维梁理论不考虑泊松效应。在 COMSOL Multiphysics 中,可以通过选择二维空间维度并选择固体力学接口,建立二维平面应力模型。
在 COMSOL Multiphysics 中计算残余应力
在这里,我们将展示如何在二维中使用固体力学接口来计算梁截面的残余应力。
使用固体力学接口的二维梁模型的屏幕截图。
根据上面的截图可知,我们定义了一些变量来评估上一节中计算出来的理论残余应力。这些值将被用于比较计算结果和理论结果。
施加的弯矩是逐渐增加的。添加一个塑性节点可以考虑到可能通过梁厚度发生的单轴塑性行为。一旦\sigma_x达到临界值\sigma_\mathrm{yield},塑性流动就开始。任何已经达到这个值的纤维在加载过程中都将保持恒定的应力状态。
在下图中,你可以看到沿横截面Y 轴的应力分布。对于深度为h_\mathrm{p}=\frac{b} {4}=0.01 \ \mathrm{m}的塑性区,施加的弯矩已由方程(4)计算出来。根据蓝色曲线,COMSOL Multiphysics 的模拟结果与该值完全吻合。红色曲线表示一个加载-卸载周期后的残余应力。值得注意的是,计算的残余应力也可以由完全弹塑性曲线(蓝色)中减去弹性曲线(绿色)得到。
弹性加载、卸载和弹塑性加载后的应力值。
将方程(7)和方程(9)定义为变量,并与 COMSOL Multiphysics 中计算的解进行比较。如前面的截图所示,你可以使用 if() 算子创建一个 “开关”,这样代表解析残余应力的两个表达式就会出现在一个表达式中。下图显示了两次加载-卸载循环后解析的和计算的残余应力。
解析的与计算的残余应力。
使用 COMSOL Multiphysics,能够对特定材料的滞后周期进行建模。如下图所示,在完全塑性行为的情况下,第二次载荷循环已经施加了一个稳定的应力-应变响应,代表每个连续的载荷循环。例如,你可以使用这些载荷循环来进行疲劳分析。
三次加载-卸载循环后的磁滞行为。
最后,但并非最不重要,让我们来找出应变硬化行为如何影响残余应力和加载-卸载循环。到目前为止,我们一直在处理一个完全塑性的材料。无论循环次数多少,也不管施加是拉伸还是压缩载荷,屈服应力都保持不变。只要不发生反向屈服,等式(5)就有效。由于卸载过程中的反向塑性变形对性能有负面影响,所以弄清楚在什么条件下可能发生反向屈服是非常重要的。
延展性材料先在一个方向受到越来越大的应力(例如拉伸),然后卸载,当在相反方向上加载时,其行为会有所不同。人们发现,现在的压缩屈服应力比拉伸时测量的要低。这就是所谓的Bauschinger 效应。同样地,初始压缩提供了一个较低的拉伸屈服应力。下图显示了两次应力循环下的这种效应:
滞后行为与运动应变硬化的关系。
现在,让我们继续讨论一个更复杂的力学过程:钣金成形工艺,在这个工艺中,残余应力非常重要。
模具金属成型
模具成型是一种广泛应用的钣金成型制造工艺。通过成型和拉伸工艺的塑性变形,工件,通常是金属板,在模具周围被永久塑形。坯料支架对坯料施加压力,导致金属板沿模具流动。
为了避免裂缝、撕裂、皱纹和过多的变薄和拉伸,你可以使用仿真方法。仿真也可以评估和克服回弹现象,即当成型过程结束,移除成形工具后,工件将如何尝试恢复其初始形状。回弹会导致成型的坯料达到意想不到的翘曲状态。为了应对这种影响,可以将板材过度弯曲。因此,模具、冲头和坯料的制造不仅要与物体的实际形状相匹配,而且要考虑到回弹。
在这项研究中,板材是由铝制成的。使用一个具有各向同性硬化的Hill正交弹塑性材料模型来描述塑性变形的特征。据观察,在拉深工艺中金属板不再表现为各向同性。随着厚度的增加塑性变形趋于减少。因此,在板材的模具成型和拉深工艺中,我们需要一种各向异性,即板材在平面内是各向异性的,而在垂直方向的强度增加,也称为横向各向异性。
下图是我们模拟的拉深工艺中使用的成型工具。
成型工具:模具显示为红色,冲头显示为蓝色,支架显示为粉红色,坯料显示为灰色。
如上所述,仿真允许处理在执行这样一个机械过程时需要考虑到的多种任务。例如,可以适当对模具和冲床的角半径进行优化,以防止金属板撕裂。为获得冲头和模具之间所需的间隙,以避免剪切或切割金属坯,使用仿真也可能是有用的。
最具挑战性的一个方面是,计算出金属板应该过度弯曲多少。当板材成型后,残余应力导致材料向其初始位置回弹,因此板材必须过度弯曲以达到预期的弯曲角度。因此,必须正确地建立残余应力模型,以免过高或过低估计回弹现象。
下面两个动画显示了钣金成型以及金属坯料的回弹现象。
在RZ 平面上的表现的回弹现象。
钣金成型仿真。
当结构承受其他力学载荷时,残余应力的叠加会降低结构的可靠性,甚至会造成不可逆的损伤。因此,必须尽可能地释放残余应力或对其进行管理,使结构能够承受可能施加的外部载荷。下图显示了杯型件拉深工艺后弯曲区域周围残留的Hill有效残余应力。
结论和拓展阅读
今天,我们研究了结构力学中的残余应力。首先,我们介绍了一个传统的定义,并将它应用在一个弯曲的梁示例中。然后使用 COMSOL Multiphysics 模拟这个弯曲的梁示例,并将结果与梁理论的解析解进行了比较。最后,我们探讨了钣金成形案例模型中残余应力的重要性。我们看到,任何力学过程都会引起残余应力,必须特别注意适当地释放它们,或者至少要确保它们不会造成任何损伤。
点击下方链接,了解更多相关产品的信息:
评论 (0)