显示活动时间: 00:00 – 00:00
搜索
近期活动
正在加载活动内容
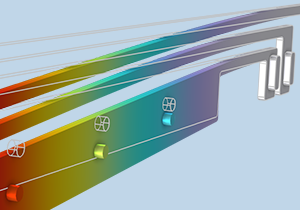
2025 年 2 月 12 日
| 07:00HKT
COMSOL 多物理场仿真简介(在线演示)
COMSOL
网络研讨会
线上

2025 年 2 月 13 日
| 07:00HKT
使用模型管理器进行仿真数据管理
COMSOL
网络研讨会
线上
显示活动 2 场,活动总数 2 场。
Date | Time | Title | Type | Host | Discipline |
---|---|---|---|---|---|
2025 年 2 月 12 日 | 07:00 | COMSOL 多物理场仿真简介(在线演示) |
网络研讨会 | COMSOL-线上 |
|
2025 年 2 月 13 日 | 07:00 | 使用模型管理器进行仿真数据管理 |
网络研讨会 | COMSOL-线上 |
|
视频培训中心
网络研讨会视频点播
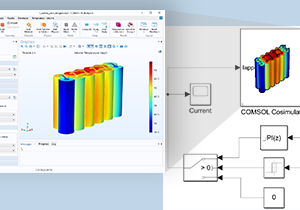
LiveLink™forMATLAB®和 LiveLink™forSimulink®功能简介
网络研讨会
Jan 09
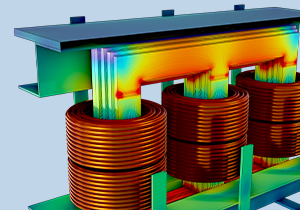
COMSOL®中的低频电磁场仿真
网络研讨会
Jan 03
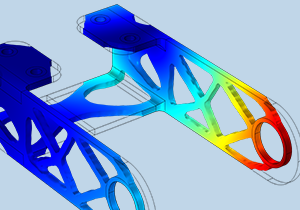
使用 COMSOL Multiphysics®优化设计
网络研讨会
Dec 26
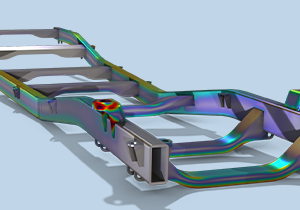
COMSOL®中的结构力学仿真
网络研讨会
Dec 19
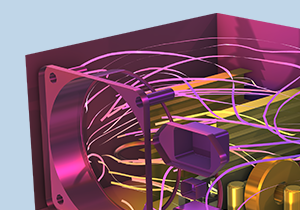
COMSOL®中的传热仿真
网络研讨会
Dec 12
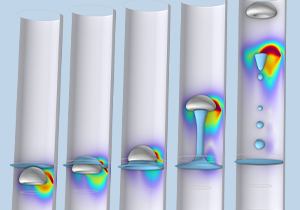
COMSOL®中的多相流仿真
网络研讨会
Dec 05

COMSOL Multiphysics®6.3 版本功能简介
网络研讨会
Nov 28
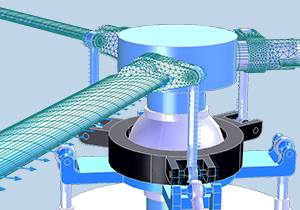
COMSOL®中的转子动力学和多体动力学仿真
网络研讨会
Nov 21

COMSOL®求解器介绍及设置方法
网络研讨会
Nov 14
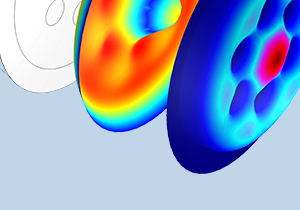
使用 COMSOL Multiphysics®模拟声学超材料
网络研讨会
Nov 07
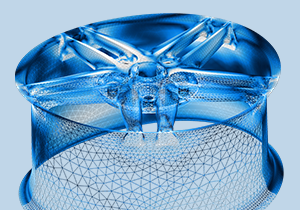
多物理场仿真结果的处理与可视化
网络研讨会
Oct 24
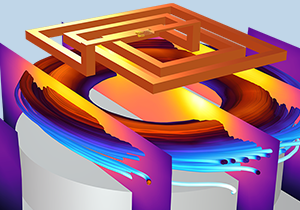
COMSOL®中的等离子体仿真
网络研讨会
Oct 17
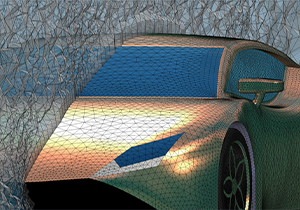
COMSOL® 网格划分功能介绍
网络研讨会
Oct 10
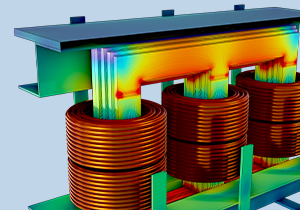
电力变压器的多物理场仿真
网络研讨会
Sep 19
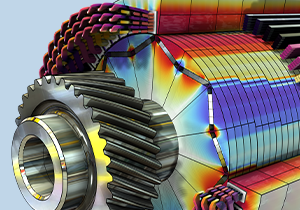
使用 COMSOL Multiphysics®仿真高性能电机
网络研讨会
Sep 12
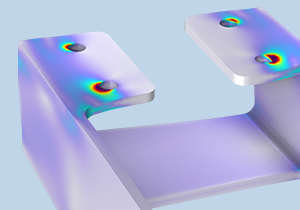
不确定性量化在多物理场仿真中的应用
网络研讨会
Sep 05
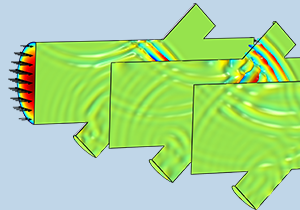
超声波及其应用的多物理场仿真
网络研讨会
Aug 29
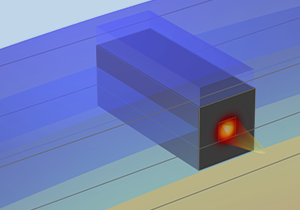
使用 COMSOL Multiphysics®模拟光电半导体
网络研讨会
Aug 15
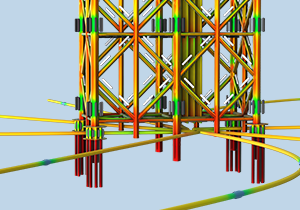
COMSOL®多物理场仿真加速数字岩心技术发展
网络研讨会
Aug 08
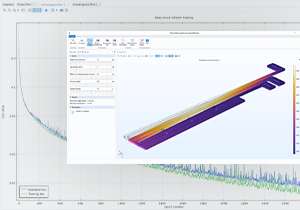
使用代理模型开发高效的 COMSOL®仿真 App
网络研讨会
Aug 01
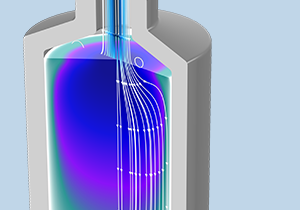
COMSOL®多物理场仿真在地热能开发中的应用
网络研讨会
Jul 25
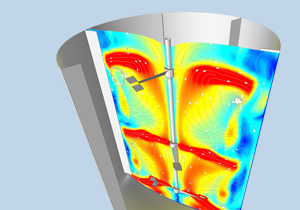
COMSOL®仿真 App 开发、部署和应用
网络研讨会
Jul 18
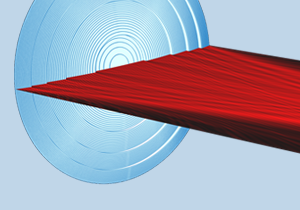
COMSOL®中的光学仿真
网络研讨会
Jul 11
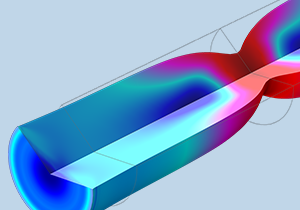
非线性结构材料参数估计
网络研讨会
Jul 04
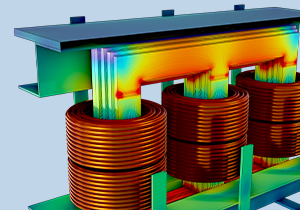
基于 COMSOL®构建电力设备的数字孪生
网络研讨会
Jun 27
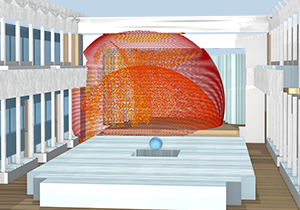
COMSOL®室内声学仿真
网络研讨会
Jun 20
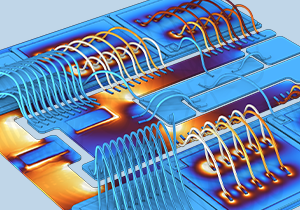
COMSOL Multiphysics®在半导体制造中的应用
网络研讨会
Jun 13
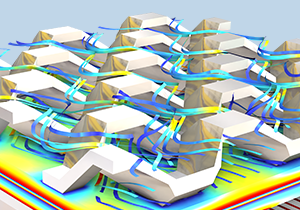
COMSOL Multiphysics®在绿氢技术中的应用
网络研讨会
Jun 06
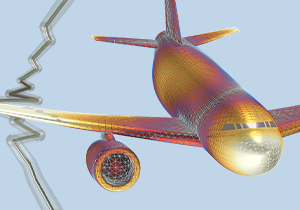
使用 COMSOL Multiphysics®模拟放电现象
网络研讨会
May 28
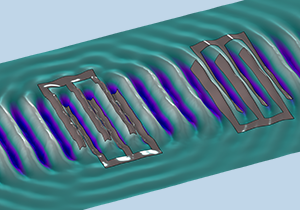
使用 COMSOL®模拟 SAW/BAW 器件
网络研讨会
May 16
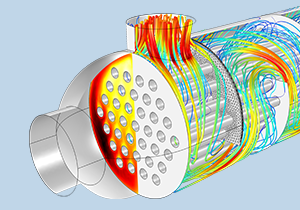
COMSOL®中的换热器仿真
网络研讨会
May 09
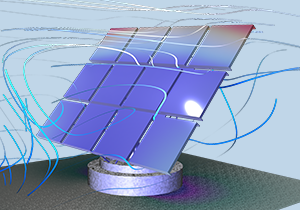
COMSOL Multiphysics®中的流固耦合仿真
网络研讨会
Apr 18
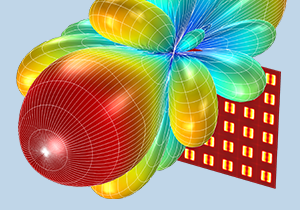
多尺度电磁波仿真
网络研讨会
Apr 11
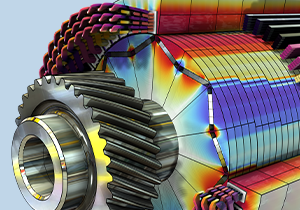
COMSOL®微执行器和微型电机仿真
网络研讨会
Apr 02
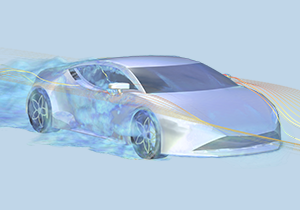
COMSOL®中的湍流仿真
网络研讨会
Mar 26
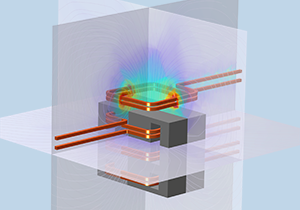
COMSOL®仿真在电力电子技术中的应用
网络研讨会
Mar 14
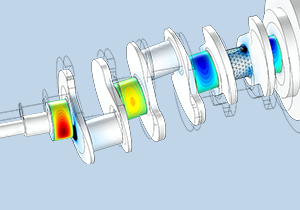
COMSOL®中的流体动压轴承仿真
网络研讨会
Mar 12
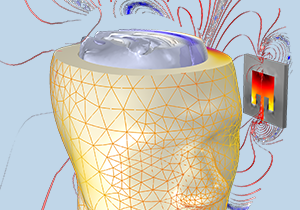
使用 COMSOL Multiphysics®模拟 EMI/EMC 现象
网络研讨会
Mar 07
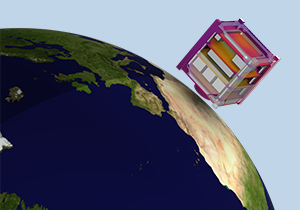
COMSOL®中的热辐射仿真
网络研讨会
Mar 05
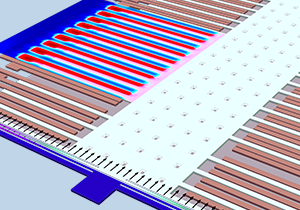
使用 COMSOL Multiphysics®模拟 MEMS 加速度计和陀螺仪
网络研讨会
Feb 29
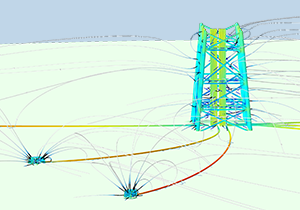
在 COMSOL Multiphysics®中模拟腐蚀及防护系统
网络研讨会
Jan 25
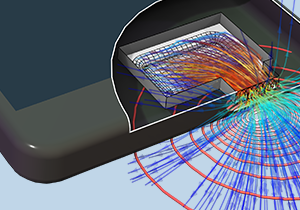
COMSOL®中的扬声器和麦克风仿真
网络研讨会
Jan 04
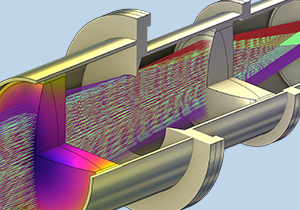
使用 COMSOL Multiphysics®进行结构-热-光学耦合分析
网络研讨会
Dec 21
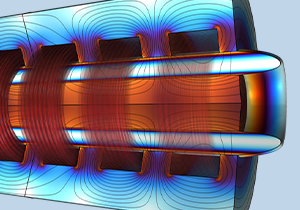
COMSOL®多物理场仿真在电气绝缘中的应用
网络研讨会
Dec 05
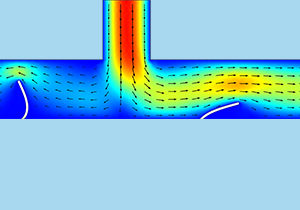
微流体器件的多物理场仿真
网络研讨会
Nov 30
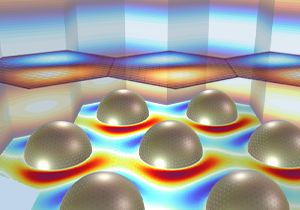
半导体制造中的晶体生长仿真
网络研讨会
Nov 28
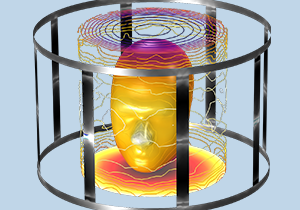
COMSOL®多物理场仿真在医疗设备研发中的应用
网络研讨会
Nov 21
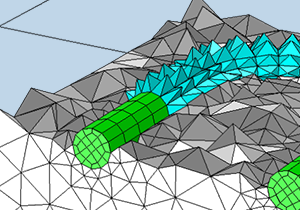
COMSOL®中的网格划分
网络研讨会
Nov 16
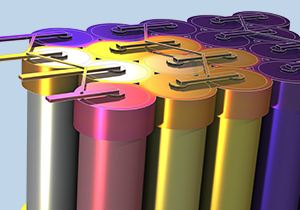
锂离子电池热失控仿真
网络研讨会
Nov 14
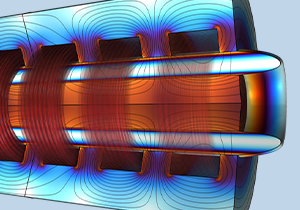
COMSOL®中的磁流体仿真
网络研讨会
Nov 09
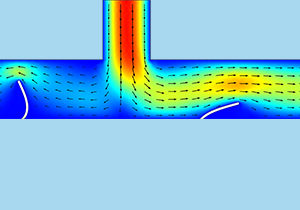
COMSOL®地下水流及多孔介质流仿真
网络研讨会
Nov 02
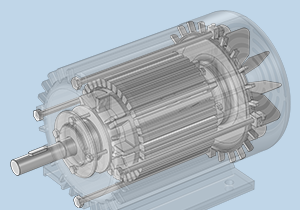
电磁噪声的仿真分析
网络研讨会
Oct 31
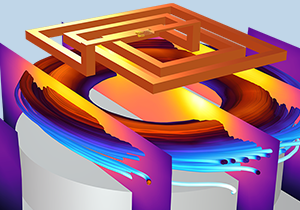
使用 COMSOL Multiphysics®仿真 PVD/CVD 薄膜沉积工艺
网络研讨会
Oct 27
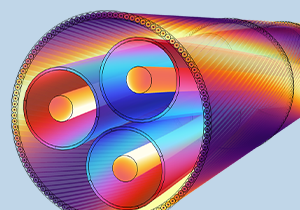
COMSOL®多物理场仿真优化电缆设计
网络研讨会
Oct 20
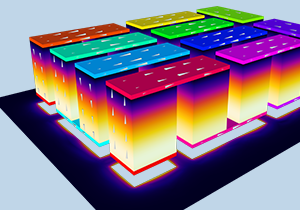
COMSOL®的求解器简介
网络研讨会
Oct 13
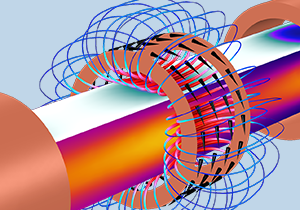
COMSOL®中的感应加热仿真
网络研讨会
Sep 26
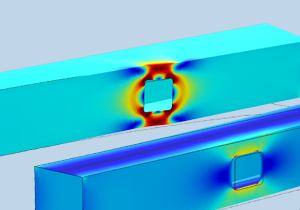
COMSOL®中的岩土力学仿真
网络研讨会
Sep 19
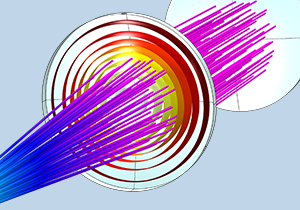
多物理场仿真在激光加工中的应用
网络研讨会
Sep 15
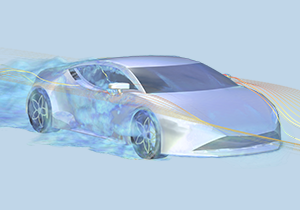
计算流体力学(CFD)多物理场仿真
网络研讨会
Sep 12
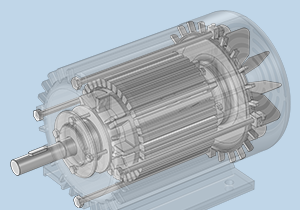
使用 COMSOL®求解大型模型
网络研讨会
Sep 08
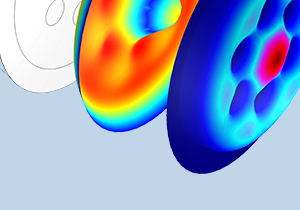
COMSOL®中的声学超材料仿真
网络研讨会
Sep 05
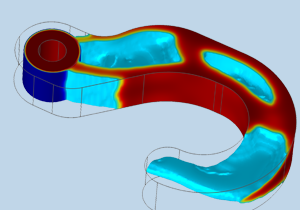
使用 COMSOL Multiphysics®进行设计优化
网络研讨会
Sep 01
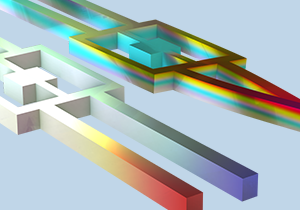
COMSOL®的压电材料和器件仿真
网络研讨会
Aug 29
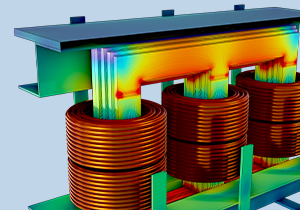
COMSOL®中的变压器仿真
网络研讨会
Aug 25
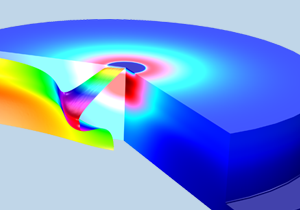
COMSOL®中的半导体器件仿真
网络研讨会
Aug 22
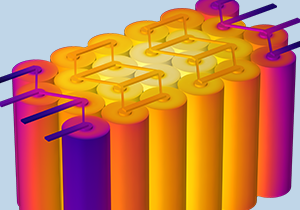
COMSOL®中的锂电池仿真
网络研讨会
Aug 18
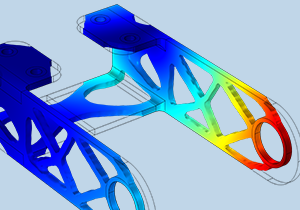
COMSOL®的结构力学仿真
网络研讨会
Aug 15
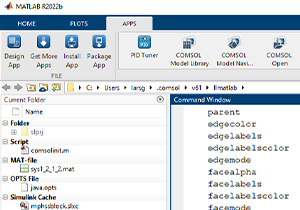
COMSOL®中的 LiveLink™forMATLAB®和 LiveLink™forSimulink®功能简介
网络研讨会
Aug 11
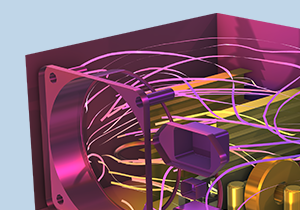
电子设备热管理的仿真分析
网络研讨会
Aug 04
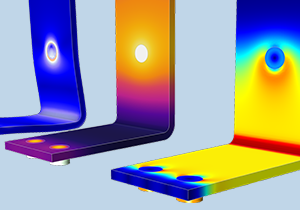
电磁损耗的仿真分析
网络研讨会
Jul 28
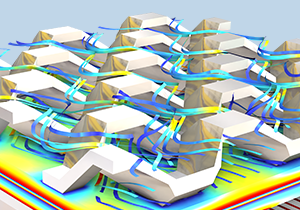
氢燃料电池与水电解槽的多物理场仿真
网络研讨会
Jul 25
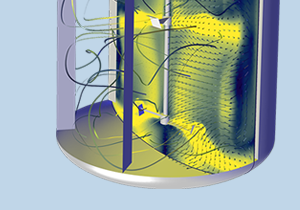
COMSOL®中的多相流仿真
网络研讨会
Jul 21
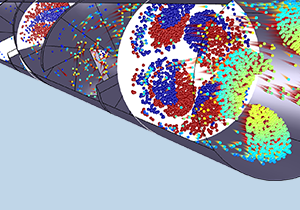
粒子追踪方法的建模仿真
网络研讨会
Jul 18
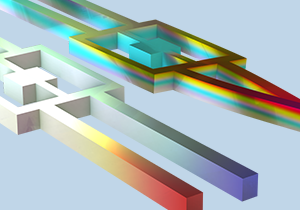
MEMS 器件的多物理场建模和仿真
网络研讨会
Jul 14
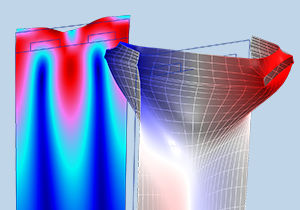
SAW 和 BAW 滤波器的建模仿真
网络研讨会
Jul 07
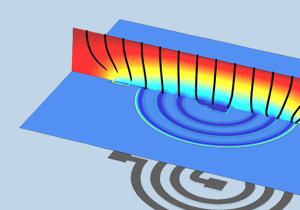
COMSOL®中的电镀仿真
网络研讨会
Jul 04
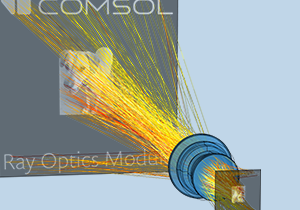
COMSOL®中的射线光学仿真
网络研讨会
Jun 30
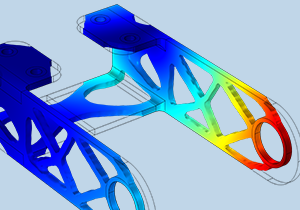
COMSOL®中的热应力仿真
网络研讨会
Jun 16
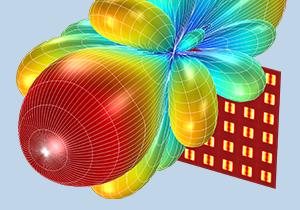
COMSOL®中的高频电磁场仿真
网络研讨会
Jun 13
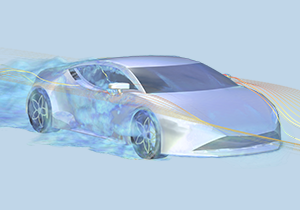
COMSOL®中的流固耦合仿真
网络研讨会
Jun 09
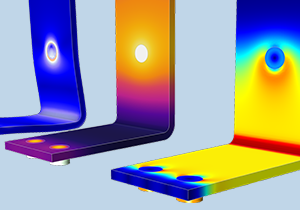
COMSOL®中的传热仿真
网络研讨会
Jun 06
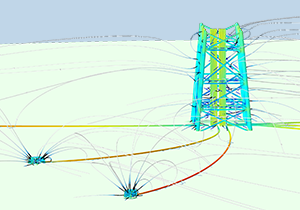
COMSOL®中的腐蚀与防护仿真
网络研讨会
Jun 02
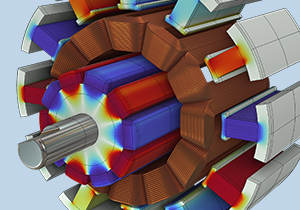
COMSOL®中的低频电磁场仿真
网络研讨会
May 23
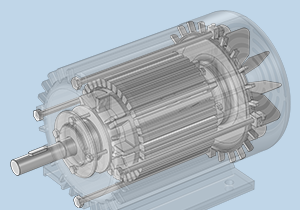
在 COMSOL®中进行 CAD 导入及几何模型处理
网络研讨会
May 19
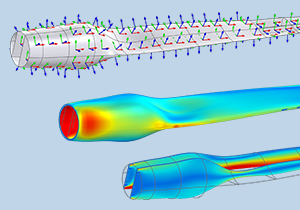
COMSOL®中的复合材料仿真
网络研讨会
May 16
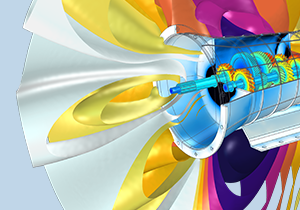
声学与振动的多物理场仿真
网络研讨会
May 12
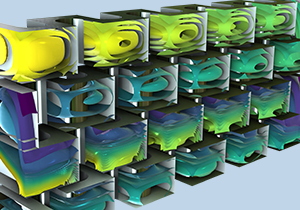
COMSOL®化学反应工程仿真
网络研讨会
Apr 18
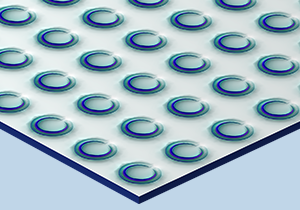
光学超材料仿真
网络研讨会
Apr 14
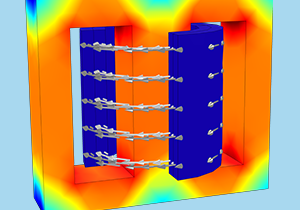
电力设备的多物理场仿真
网络研讨会
Apr 07
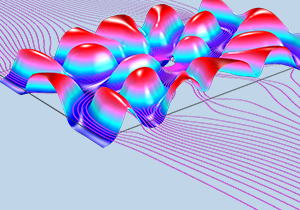
在 COMSOL®中使用自定义函数建模
网络研讨会
Mar 31
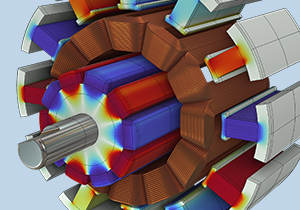
COMSOL®6.1 电磁模拟新功能
网络研讨会
Mar 24
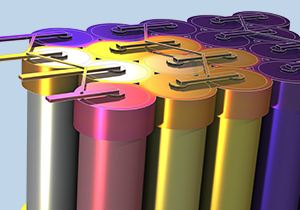
COMSOL®6.1 电池模块新功能
网络研讨会
Mar 17
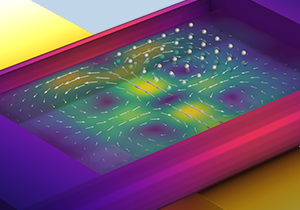
COMSOL®中的声流仿真
网络研讨会
Mar 10
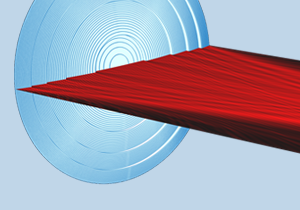
COMSOL Multiphysics®波动光学仿真
网络研讨会
Mar 07
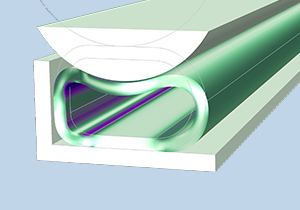
COMSOL®6.1 结构力学模块新功能
网络研讨会
Mar 03
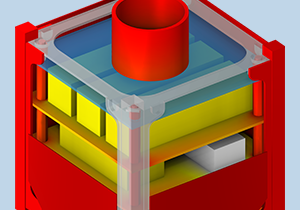
如何使用 COMSOL®分析航天器热性能
网络研讨会
Feb 24
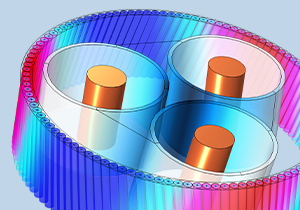
COMSOL®6.1 模型管理器和 App 开发器新功能介绍
网络研讨会
Feb 17
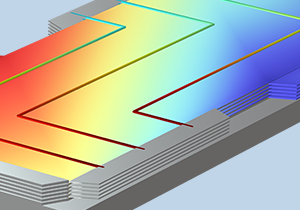
COMSOL®6.1 燃料电池和电解槽模块新功能
网络研讨会
Feb 10
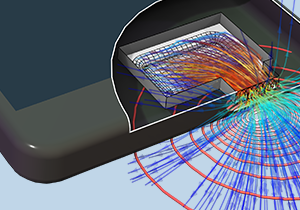
COMSOL®6.1 声学模块新功能
网络研讨会
Feb 03
显示活动 6 场,活动总数 99 场。
Date | Title | Type | Host | Discipline |
---|---|---|---|---|
Jan 09 | LiveLink™forMATLAB®和 LiveLink™forSimulink®功能简介 |
网络研讨会 | COMSOL-线上 |
|
Jan 03 | COMSOL®中的低频电磁场仿真 |
网络研讨会 | COMSOL-线上 |
|
Dec 26 | 使用 COMSOL Multiphysics®优化设计 |
网络研讨会 | COMSOL-线上 |
|
Dec 19 | COMSOL®中的结构力学仿真 |
网络研讨会 | COMSOL-线上 |
|
Dec 12 | COMSOL®中的传热仿真 |
网络研讨会 | COMSOL-线上 |
|
Dec 05 | COMSOL®中的多相流仿真 |
网络研讨会 | COMSOL-线上 |
|
Nov 28 | COMSOL Multiphysics®6.3 版本功能简介 |
网络研讨会 | COMSOL-线上 |
|
Nov 21 | COMSOL®中的转子动力学和多体动力学仿真 |
网络研讨会 | COMSOL-线上 |
|
Nov 14 | COMSOL®求解器介绍及设置方法 |
网络研讨会 | COMSOL-线上 |
|
Nov 07 | 使用 COMSOL Multiphysics®模拟声学超材料 |
网络研讨会 | COMSOL-线上 |
|
Oct 24 | 多物理场仿真结果的处理与可视化 |
网络研讨会 | COMSOL-线上 |
|
Oct 17 | COMSOL®中的等离子体仿真 |
网络研讨会 | COMSOL-线上 |
|
Oct 10 | COMSOL® 网格划分功能介绍 |
网络研讨会 | COMSOL-线上 |
|
Sep 19 | 电力变压器的多物理场仿真 |
网络研讨会 | COMSOL-线上 |
|
Sep 12 | 使用 COMSOL Multiphysics®仿真高性能电机 |
网络研讨会 | COMSOL-线上 |
|
Sep 05 | 不确定性量化在多物理场仿真中的应用 |
网络研讨会 | COMSOL-线上 |
|
Aug 29 | 超声波及其应用的多物理场仿真 |
网络研讨会 | COMSOL-线上 |
|
Aug 15 | 使用 COMSOL Multiphysics®模拟光电半导体 |
网络研讨会 | COMSOL-线上 |
|
Aug 08 | COMSOL®多物理场仿真加速数字岩心技术发展 |
网络研讨会 | COMSOL-线上 |
|
Aug 01 | 使用代理模型开发高效的 COMSOL®仿真 App |
网络研讨会 | COMSOL-线上 |
|
Jul 25 | COMSOL®多物理场仿真在地热能开发中的应用 |
网络研讨会 | COMSOL-线上 |
|
Jul 18 | COMSOL®仿真 App 开发、部署和应用 |
网络研讨会 | COMSOL-线上 |
|
Jul 11 | COMSOL®中的光学仿真 |
网络研讨会 | COMSOL-线上 |
|
Jul 04 | 非线性结构材料参数估计 |
网络研讨会 | COMSOL-线上 |
|
Jun 27 | 基于 COMSOL®构建电力设备的数字孪生 |
网络研讨会 | COMSOL-线上 |
|
Jun 20 | COMSOL®室内声学仿真 |
网络研讨会 | COMSOL-线上 |
|
Jun 13 | COMSOL Multiphysics®在半导体制造中的应用 |
网络研讨会 | COMSOL-线上 |
|
Jun 06 | COMSOL Multiphysics®在绿氢技术中的应用 |
网络研讨会 | COMSOL-线上 |
|
May 28 | 使用 COMSOL Multiphysics®模拟放电现象 |
网络研讨会 | COMSOL-线上 |
|
May 16 | 使用 COMSOL®模拟 SAW/BAW 器件 |
网络研讨会 | COMSOL-线上 |
|
May 09 | COMSOL®中的换热器仿真 |
网络研讨会 | COMSOL-线上 |
|
Apr 18 | COMSOL Multiphysics®中的流固耦合仿真 |
网络研讨会 | COMSOL-线上 |
|
Apr 11 | 多尺度电磁波仿真 |
网络研讨会 | COMSOL-线上 |
|
Apr 02 | COMSOL®微执行器和微型电机仿真 |
网络研讨会 | COMSOL-线上 |
|
Mar 26 | COMSOL®中的湍流仿真 |
网络研讨会 | COMSOL-线上 |
|
Mar 14 | COMSOL®仿真在电力电子技术中的应用 |
网络研讨会 | COMSOL-线上 |
|
Mar 12 | COMSOL®中的流体动压轴承仿真 |
网络研讨会 | COMSOL-线上 |
|
Mar 07 | 使用 COMSOL Multiphysics®模拟 EMI/EMC 现象 |
网络研讨会 | COMSOL-线上 |
|
Mar 05 | COMSOL®中的热辐射仿真 |
网络研讨会 | COMSOL-线上 |
|
Feb 29 | 使用 COMSOL Multiphysics®模拟 MEMS 加速度计和陀螺仪 |
网络研讨会 | COMSOL-线上 |
|
Jan 25 | 在 COMSOL Multiphysics®中模拟腐蚀及防护系统 |
网络研讨会 | COMSOL-线上 |
|
Jan 04 | COMSOL®中的扬声器和麦克风仿真 |
网络研讨会 | COMSOL-线上 |
|
Dec 21 | 使用 COMSOL Multiphysics®进行结构-热-光学耦合分析 |
网络研讨会 | COMSOL-线上 |
|
Dec 05 | COMSOL®多物理场仿真在电气绝缘中的应用 |
网络研讨会 | COMSOL-线上 |
|
Nov 30 | 微流体器件的多物理场仿真 |
网络研讨会 | COMSOL-线上 |
|
Nov 28 | 半导体制造中的晶体生长仿真 |
网络研讨会 | COMSOL-线上 |
|
Nov 21 | COMSOL®多物理场仿真在医疗设备研发中的应用 |
网络研讨会 | COMSOL-线上 |
|
Nov 16 | COMSOL®中的网格划分 |
网络研讨会 | COMSOL-线上 |
|
Nov 14 | 锂离子电池热失控仿真 |
网络研讨会 | COMSOL-线上 |
|
Nov 09 | COMSOL®中的磁流体仿真 |
网络研讨会 | COMSOL-线上 |
|
Nov 02 | COMSOL®地下水流及多孔介质流仿真 |
网络研讨会 | COMSOL-线上 |
|
Oct 31 | 电磁噪声的仿真分析 |
网络研讨会 | COMSOL-线上 |
|
Oct 27 | 使用 COMSOL Multiphysics®仿真 PVD/CVD 薄膜沉积工艺 |
网络研讨会 | COMSOL-线上 |
|
Oct 20 | COMSOL®多物理场仿真优化电缆设计 |
网络研讨会 | COMSOL-线上 |
|
Oct 13 | COMSOL®的求解器简介 |
网络研讨会 | COMSOL-线上 |
|
Sep 26 | COMSOL®中的感应加热仿真 |
网络研讨会 | COMSOL-线上 |
|
Sep 19 | COMSOL®中的岩土力学仿真 |
网络研讨会 | COMSOL-线上 |
|
Sep 15 | 多物理场仿真在激光加工中的应用 |
网络研讨会 | COMSOL-线上 |
|
Sep 12 | 计算流体力学(CFD)多物理场仿真 |
网络研讨会 | COMSOL-线上 |
|
Sep 08 | 使用 COMSOL®求解大型模型 |
网络研讨会 | COMSOL-线上 |
|
Sep 05 | COMSOL®中的声学超材料仿真 |
网络研讨会 | COMSOL-线上 |
|
Sep 01 | 使用 COMSOL Multiphysics®进行设计优化 |
网络研讨会 | COMSOL-线上 |
|
Aug 29 | COMSOL®的压电材料和器件仿真 |
网络研讨会 | COMSOL-线上 |
|
Aug 25 | COMSOL®中的变压器仿真 |
网络研讨会 | COMSOL-线上 |
|
Aug 22 | COMSOL®中的半导体器件仿真 |
网络研讨会 | COMSOL-线上 |
|
Aug 18 | COMSOL®中的锂电池仿真 |
网络研讨会 | COMSOL-线上 |
|
Aug 15 | COMSOL®的结构力学仿真 |
网络研讨会 | COMSOL-线上 |
|
Aug 11 | COMSOL®中的 LiveLink™forMATLAB®和 LiveLink™forSimulink®功能简介 |
网络研讨会 | COMSOL-线上 |
|
Aug 04 | 电子设备热管理的仿真分析 |
网络研讨会 | COMSOL-线上 |
|
Jul 28 | 电磁损耗的仿真分析 |
网络研讨会 | COMSOL-线上 |
|
Jul 25 | 氢燃料电池与水电解槽的多物理场仿真 |
网络研讨会 | COMSOL-线上 |
|
Jul 21 | COMSOL®中的多相流仿真 |
网络研讨会 | COMSOL-线上 |
|
Jul 18 | 粒子追踪方法的建模仿真 |
网络研讨会 | COMSOL-线上 |
|
Jul 14 | MEMS 器件的多物理场建模和仿真 |
网络研讨会 | COMSOL-线上 |
|
Jul 07 | SAW 和 BAW 滤波器的建模仿真 |
网络研讨会 | COMSOL-线上 |
|
Jul 04 | COMSOL®中的电镀仿真 |
网络研讨会 | COMSOL-线上 |
|
Jun 30 | COMSOL®中的射线光学仿真 |
网络研讨会 | COMSOL-线上 |
|
Jun 16 | COMSOL®中的热应力仿真 |
网络研讨会 | COMSOL-线上 |
|
Jun 13 | COMSOL®中的高频电磁场仿真 |
网络研讨会 | COMSOL-线上 |
|
Jun 09 | COMSOL®中的流固耦合仿真 |
网络研讨会 | COMSOL-线上 |
|
Jun 06 | COMSOL®中的传热仿真 |
网络研讨会 | COMSOL-线上 |
|
Jun 02 | COMSOL®中的腐蚀与防护仿真 |
网络研讨会 | COMSOL-线上 |
|
May 23 | COMSOL®中的低频电磁场仿真 |
网络研讨会 | COMSOL-线上 |
|
May 19 | 在 COMSOL®中进行 CAD 导入及几何模型处理 |
网络研讨会 | COMSOL-线上 |
|
May 16 | COMSOL®中的复合材料仿真 |
网络研讨会 | COMSOL-线上 |
|
May 12 | 声学与振动的多物理场仿真 |
网络研讨会 | COMSOL-线上 |
|
Apr 18 | COMSOL®化学反应工程仿真 |
网络研讨会 | COMSOL-线上 |
|
Apr 14 | 光学超材料仿真 |
网络研讨会 | COMSOL-线上 |
|
Apr 07 | 电力设备的多物理场仿真 |
网络研讨会 | COMSOL-线上 |
|
Mar 31 | 在 COMSOL®中使用自定义函数建模 |
网络研讨会 | COMSOL-线上 |
|
Mar 24 | COMSOL®6.1 电磁模拟新功能 |
网络研讨会 | COMSOL-线上 |
|
Mar 17 | COMSOL®6.1 电池模块新功能 |
网络研讨会 | COMSOL-线上 |
|
Mar 10 | COMSOL®中的声流仿真 |
网络研讨会 | COMSOL-线上 |
|
Mar 07 | COMSOL Multiphysics®波动光学仿真 |
网络研讨会 | COMSOL-线上 |
|
Mar 03 | COMSOL®6.1 结构力学模块新功能 |
网络研讨会 | COMSOL-线上 |
|
Feb 24 | 如何使用 COMSOL®分析航天器热性能 |
网络研讨会 | COMSOL-线上 |
|
Feb 17 | COMSOL®6.1 模型管理器和 App 开发器新功能介绍 |
网络研讨会 | COMSOL-线上 |
|
Feb 10 | COMSOL®6.1 燃料电池和电解槽模块新功能 |
网络研讨会 | COMSOL-线上 |
|
Feb 03 | COMSOL®6.1 声学模块新功能 |
网络研讨会 | COMSOL-线上 |
|
显示活动 99 场,活动总数 99 场。