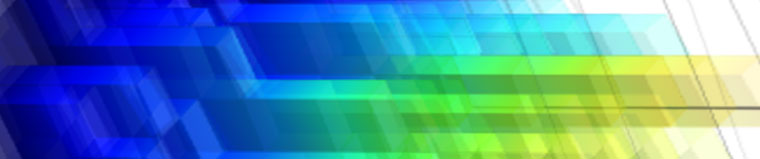
材料疲劳
什么是材料疲劳?
材料疲劳 是一种结构在循环载荷作用下出现失效的现象。即使材料受到的应力远低于材料的静态强度,也可能会发生这种类型的结构损伤。疲劳是造成机械结构失效最常见的原因。
组件在反复载荷作用下导致最终失效的过程,可以分为三个阶段:
- 在多次循环作用下,材料损伤在微观层面不断发展,直到形成宏观裂纹。
- 在每次循环中,宏观裂纹都会不断增长,直至达到临界长度。
- 当出现裂纹的组件无法继续承受峰值载荷时,就会发生断裂。
在某些应用中,我们无法观察到第二阶段的变化。这种情况下,裂纹在微观尺度上快速增长,导致组件突然失效。
后两个阶段的细节通常属于断裂力学 领域的研究内容。疲劳 这一术语主要适用于第一阶段。然而,这些学科之间存在一些重叠,测得的疲劳循环次数往往还包含后两个阶段。由于组件的大部分寿命都消耗在了出现宏观裂纹之前,因此,大多数设计方案都会尽可能避免出现此类损伤。
疲劳变量
在非恒定外部载荷的影响下,材料的状态还会随时间发生变化。材料中某个点的状态可以通过许多不同的变量(例如应力、应变或能耗)来描述,而疲劳过程通常被认为是由一类特定的变量控制。人们将载荷循环 定义为:所研究变量的一个峰值到下一个峰值的持续时间。通常情况下,不同的循环有着不同的幅值。不过,在粗浅的讨论中,我们可以假设控制疲劳状态的变量在每个载荷循环的开始和结束点都具有相同的值。在弹性材料中,循环载荷会引起周期性的循环应力响应。对于这种情况,载荷循环的定义非常简单。下图对此进行了说明,其中,控制疲劳状态的变量是应力。
在一个载荷循环中,应力在最大应力 \sigma_{\textrm{max}} 与最小应力 \sigma_{\textrm{min}} 之间变化。在研究疲劳时,通常使用应力幅值 \sigma_{\textrm{a}} 和平均应力 \sigma_{\textrm{m}} 来定义应力的变化。此外,用于定义应力范围 \Delta\sigma 的变量和 R 值常用来描述应力循环。各个疲劳应力变量之间的关系可以表示为,
在描述疲劳损伤时,最重要的参数是应力幅值。然而,如果要进行详细分析,还必须考虑平均应力。其中,平均拉应力会增加材料对疲劳的敏感性,而平均压应力则会增大材料的应力幅值。
材料对一系列载荷循环的响应与外部载荷的性质高度相关,外加载荷既可以是周期性的,也可以是随机的,甚至还可能是可重复的块组成。对于后两种情况,对载荷循环的描述比纯周期性的情况相对更加复杂,需要一些特殊处理。
低周和高周疲劳
疲劳分析并非总是基于应力响应。然而,纵观这一分支学科的发展史,由于大部分研究都是借助基于应力的模型来进行的,因此,这在过去一直备受关注。根据产生裂纹所需的载荷循环次数,人们习惯将疲劳分为低周疲劳(LCF)和高周疲劳(HCF)。两者之间的界限并不明确,但通常以数万次循环作为区分的依据。基本的物理原理是,在高周疲劳情况下,应力足够低,因此应力-应变关系可以被认为是弹性的。在分析高周疲劳时,应力范围通常用于描述局部状态。另外,在分析低周疲劳时,应变范围或耗散能量也是常用的选择。
疲劳模型
材料疲劳领域的研究最早开始于 19 世纪,这一领域的持续发展产生了许多疲劳预测方法。其中一个经典模型就是 S-N 曲线。这一曲线将材料失效前所经历的循环次数(即寿命)N 与单轴加载的应力幅值关联起来。总的趋势是,降低应力幅值,可以获得更长的材料使用寿命。通常来说,这种相关性非常强,可以达到应力幅值降低 10% 就能够将使用寿命延长 50%。某些材料在疲劳试验中表现出了应力阈值,称为疲劳极限,当应力低于该阈值时,不会出现疲劳损伤,组件的运行寿命可以无限长。不过,并非所有材料都有疲劳极限。因此,有些材料即使在低水平应力作用下,也会因疲劳而失效。
在多轴加载的情况下,外部载荷的方向或位置各不相同,从而使结构在不同的方向上发生变形。这就意味着,在每次计算时都必须计算全应力或全应变张量,而非一个标量值。我们通常可以使用临界面法来实现,具体做法是通过研究空间中的多个平面,找出预计会产生初始疲劳的临界面。
对于随机载荷,由于每次循环都不同,因此不能用单一的应力幅值来描述应力循环。为了合理预测疲劳,必须将全应力历史转换为应力谱,使之在下一步分析中与疲劳相关。我们可以使用雨流计数法来定义一组具有相应平均应力的应力幅值。Palmgren-Miner 线性损伤法则是在这样一组不同应力水平下用来预测疲劳的常用方法。
在振动疲劳中经常会出现随机载荷,在此过程中,结构承受的是动载荷。由于应力与激发频率相关,因此可以使用功率谱密度等方法在频域中进行疲劳评估。
某些材料的疲劳寿命受微结构缺陷数量的影响非常大。对这些材料来说,缺陷的位置对组件寿命有着直接的影响。例如,与远离应力集中区的缺陷相比,位于应力集中区附近的缺陷会显著缩短组件的寿命。我们可以使用概率统计方法来处理这种类型的应用。
当我们在选择模型进行疲劳预测时,没有任何放之四海而皆准的模型可以直接使用,每个模型的适用性都取决于所使用的材料和载荷类型。然而,我们可以通过一些简单的定性问题(如博客文章“疲劳模型的选择”中所述)来缩小适用模型的选择范围。
疲劳材料数据
疲劳评估不仅需要疲劳模型,还需要材料数据。每个模型都需要一组不同的材料参数,这些参数可以通过材料测试获取。疲劳试验是一个非常耗时的过程,这是因为在材料表现出疲劳特征之前,每一次试验都需要循环很多次。例如,在高周疲劳中,一个试样可能要经历 100 万次载荷循环才会失效。
此外,微观结构对疲劳灵敏度的影响也会使试验结果不统一。出现这种情况的原因是,材料在微力学层面上不均匀。以合金材料为例,结晶颗粒和颗粒边界会导致应力集中。在金属铸件的凝固过程中,甚至还可能形成孔隙。因此,局部尺度上的应变值可能远大于宏观层面上的平均值,并可能导致晶体内部发生位错。由于这种微力学层面上的位置不规则或多或少是随机分布的,因此特定类型的组件所能承受的载荷循环次数存在很大的分散性,即使在均匀的外部载荷作用下也是如此。基于以上原因,我们需要对大量的试样进行测试,才能得到可靠的疲劳数据。
在评估测试结果时,我们还需要考虑统计效应。以下是此类效应的两个示例:
- 如果两组不同直径的钢筋在相同的表观应力下进行拉伸测试,直径较大的一组钢筋的寿命可能较短。原因在于,材料的体积越大,出现某种尺寸的微观缺陷的可能性就越大。
- 如果对同一类型的钢筋分别进行拉伸载荷和弯曲载荷测试,对其施加相同的峰值应力,受弯曲载荷作用的钢筋的寿命可能更长。在弯曲过程中,只有一小部分体积的材料会承受最大应力。
除此之外,表面处理和工作环境等因素也会进一步影响材料的疲劳强度。
在将测量数据转换为某种结构的许用值时,必须考虑所有这些因素的综合效应,以及材料失效的潜在风险可能带来的后果。
发布日期:2016 年 3 月 15 日上次修改日期:2017 年 2 月 21 日