3D Magneto-Thermo-Hydrodynamic Modeling of Arc Welding
In the nuclear industry, and particularly at Framatome, mastery of welding processes is essential. Framatome is one of the world leaders in this field and wants to improve even more. The work presented focuses on improving the TIG (Tungsten Inert Gas) welding process, and more specifically on its pulsed mode. Improved understanding of the physical phenomena and their influence on the melting pool properties of pulsed TIG process with filler metal will allow us to: - anticipate defects (lack of penetration, migration of chemical species, etc.) - optimize process parameters (electric current, travel speed, etc.) - justify the quality of welded components. To do this, we decided to develop predictive models to simulate the TIG process with filler metal. This is the goal of the thesis. This presentation will present 3D magneto-thermo-hydrodynamic model with coupling between the arc column and the melting pool, developed in the finite element software COMSOL Multiphysics®. This model can be used, for example, to analyse the dynamic behaviour of the melting pool. A multi-scale approach is adopted to optimize calculation times. A 2D axisymmetric model is used to solve the electromagnetic equations. These results are synchronously integrated into a 3D thermo-hydraulic model, allowing electromagnetic effects to be taken into account. The ALE (Arbitrary Lagrangian-Eulerian) moving mesh method is used to simulate the deformation of the melting pool under the effect of arc pressure. A numerical artefact has been developed to optimize control of the moving interface in areas of high viscosity gradient.
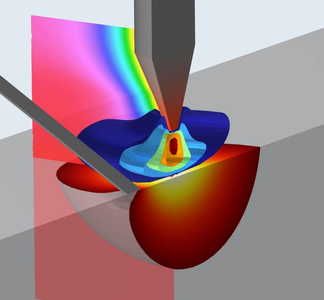
下载
- LeGalLaSalle_5051_poster.pdf - 1.12MB